Nationwide In-House Commercial kitchen Flooring installation
Craftsman Concrete Floors specializes in installing commercial flooring systems designed for exceptional durability and minimal maintenance. From our corporate headquarters in Dallas, Texas, we offer nationwide in-house service. As one of America’s premier commercial flooring installers, we deliver manufacturer-warrantied solutions trusted by leading companies nationwide. Our seasoned industry experts bring decades of experience in flooring installation, materials manufacturing, and product innovation—ensuring unmatched precision and craftsmanship.
Commercial kitchen flooring must withstand harsh conditions, including frequent temperature swings, chemical exposure, and heavy foot traffic. Urethane cement and poured epoxy flooring systems are specifically engineered to meet these demanding requirements, providing superior thermal shock resistance, chemical protection, and long-term durability. Proper installation of these seamless flooring solutions ensures compliance with local health and safety regulations, reduces maintenance costs, and helps maintain hygienic conditions essential for food preparation environments. Selecting the appropriate flooring system is critical to protecting public health and ensuring operational efficiency in commercial kitchen settings.
Discuss Your Project & Get a Quote
Speak with an expert and get a no obligation estimate. A Craftsman Specialist will reach out within one business day.
Our Clients
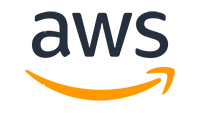
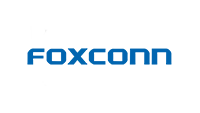
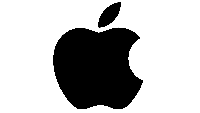
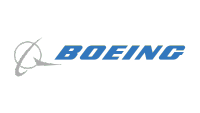
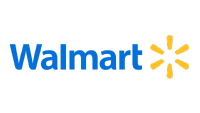
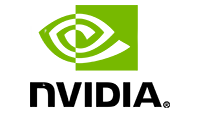
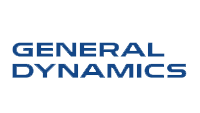
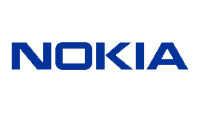
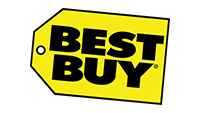
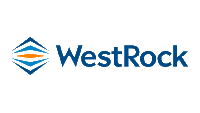
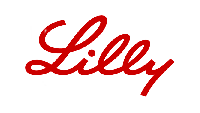

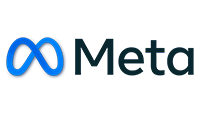
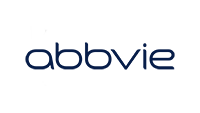
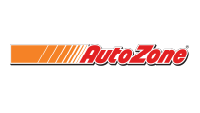
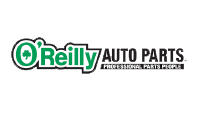
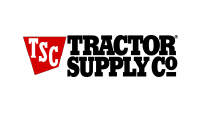
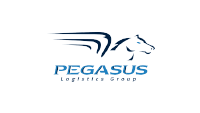
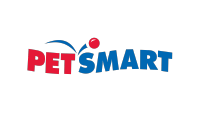
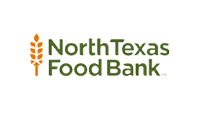
Health Code Requirements for Commercial kitchens
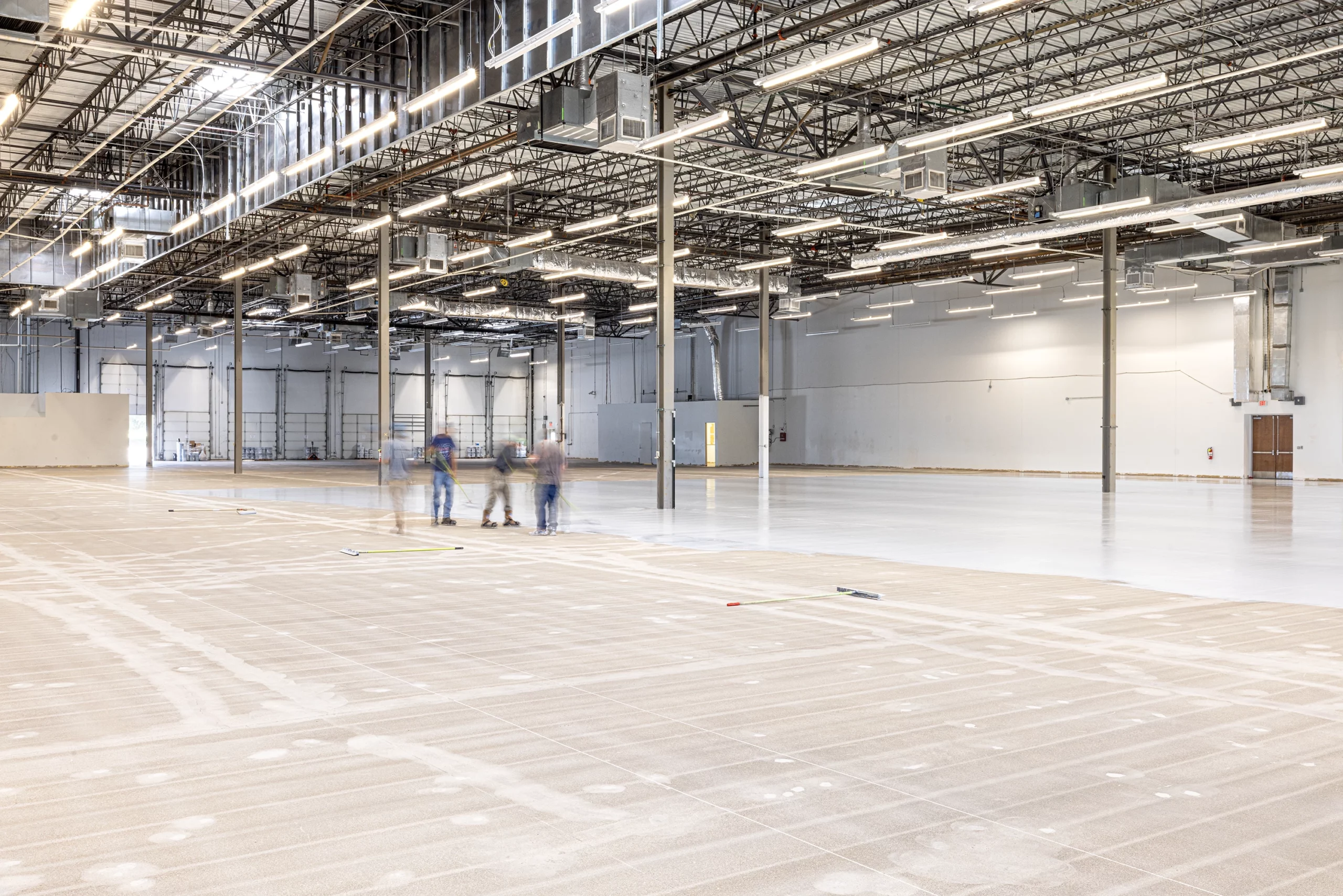
General Requirements
According to most local health code regulations, commercial kitchen flooring must be smooth, durable, and easy to clean. Floors must not have cracks, open seams, or rough textures. Surfaces must allow effective cleaning and sanitation. Floors should stay free from damage to ensure proper cleanliness. Durable materials help kitchens stay sanitary and safe. Smooth flooring helps prevent buildup of dirt and bacteria. Commercial kitchens must keep all flooring surfaces in good condition and easy to maintain.
Health codes often specify that flooring in food prep areas, dishwashing stations, walk-in refrigeration units, and other wet areas must use materials that do not absorb moisture. Floors must also resist grease and food residue. Carpet or absorbent flooring materials are not allowed in these locations. This rule helps keep surfaces clean, dry, and safe for food handling. Proper flooring helps protect against moisture buildup and contamination. Nonabsorbent materials help prevent food particles and liquids from soaking into the floor, reducing the risk of bacteria growth.
Health codes mandate commercial kitchens use slip-resistant flooring to protect workers from slips and falls. Floors must remain safe, even if they become wet or oily. Following these flooring guidelines helps businesses avoid accidents, ensures employee safety, and meets required health standards. Clearly, adhering to proper flooring requirements is essential to keeping your kitchen safe and compliant with food safety regulations.
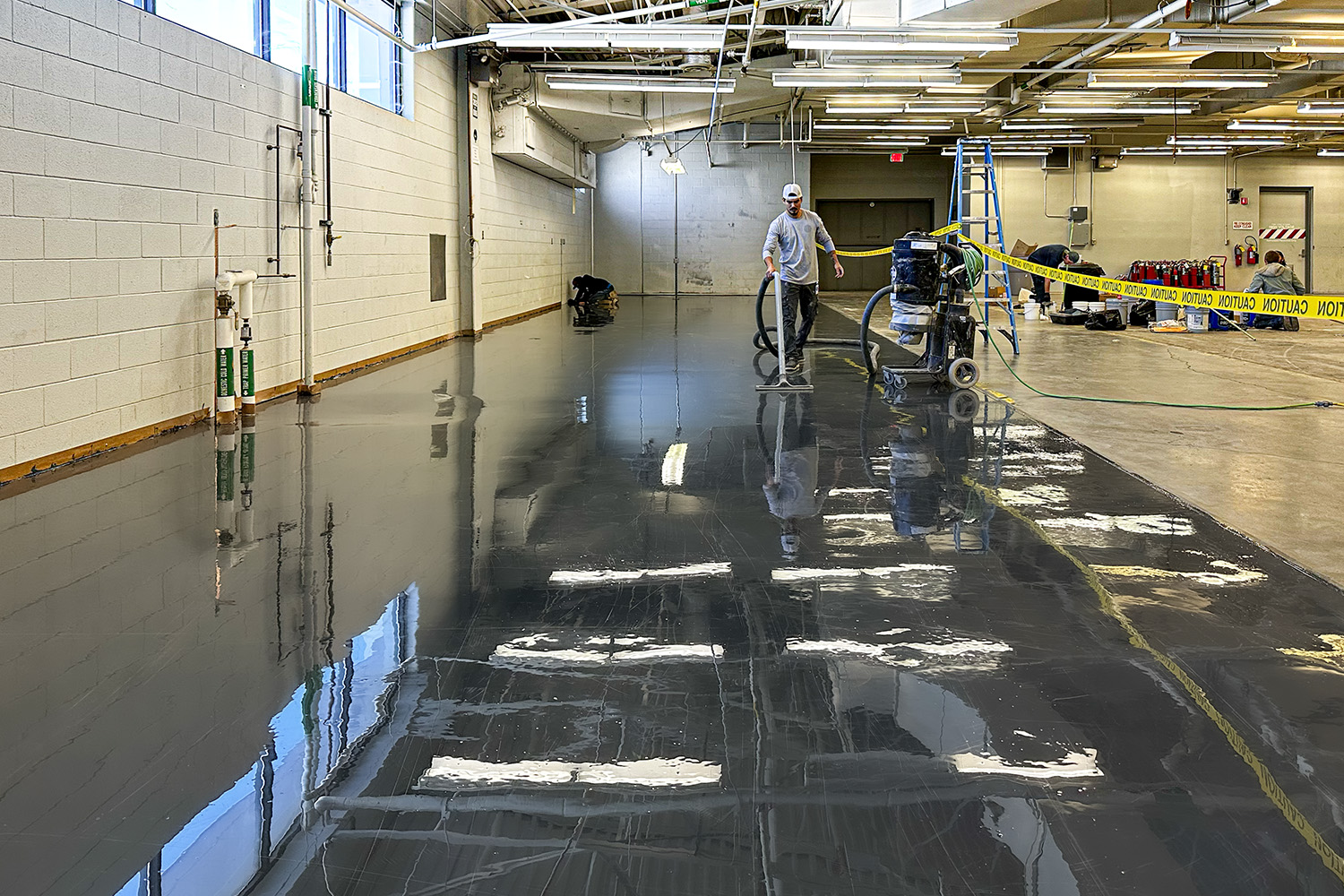
Approved Flooring Materials
Health codes approve commercial kitchen flooring materials such as urethane cement, quarry tile, ceramic tile, poured epoxy resin flooring, and vinyl composite tile (VCT) with sealed seams. Urethane cement is specifically recommended because it is durable, easy to clean, and resistant to thermal shock.
Floor Drain Requirements
Local health codes require floor drains in food preparation spaces, dishwashing areas, and zones with frequent cleaning or liquid discharge. Floors must slope toward these drains at a minimum rate of 1/8 to 1/4 inch per foot. This helps ensure proper drainage and prevents water from pooling or standing, maintaining sanitary and safe kitchen conditions for commercial settings.
Coving at Floor and Wall Junctures
Commercial kitchens must have coved base junctures where floors meet walls. Coving needs to be smooth, nonabsorbent, and easy to clean. The recommended radius for coving is at least 3/8 inch. This helps prevent dirt buildup and makes sanitation easier, meeting required health standards.
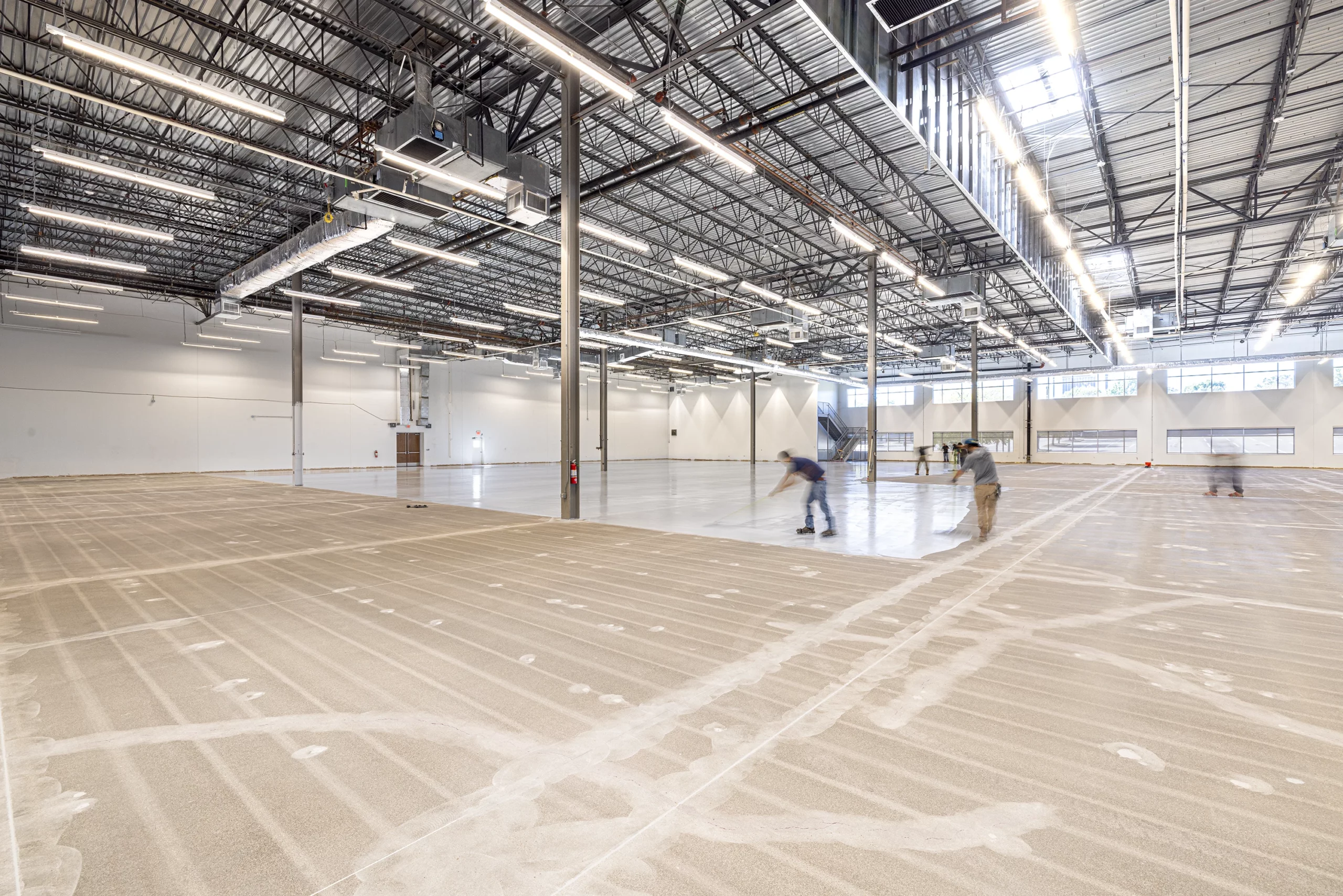
Version of FDA Code Used as Model
Most local health regulations for commercial food establishments follow the FDA Food Code 2022 Edition. This code sets standards for commercial kitchen flooring, ensuring surfaces are smooth, durable, easy to clean, and non-absorbent.
Other health Code Provisions
Health codes require commercial kitchens to keep documentation on flooring materials and cleaning procedures available for inspection. Flooring must always remain in good condition. Any worn or damaged flooring must be repaired or replaced promptly to meet health code standards. Kitchen floors should be smooth, non-absorbent, and easy to clean. In most localities, inspectors regularly check flooring to ensure compliance. Proper flooring helps prevent contamination and supports safe food preparation. Commercial kitchens must follow guidelines closely to pass inspections.
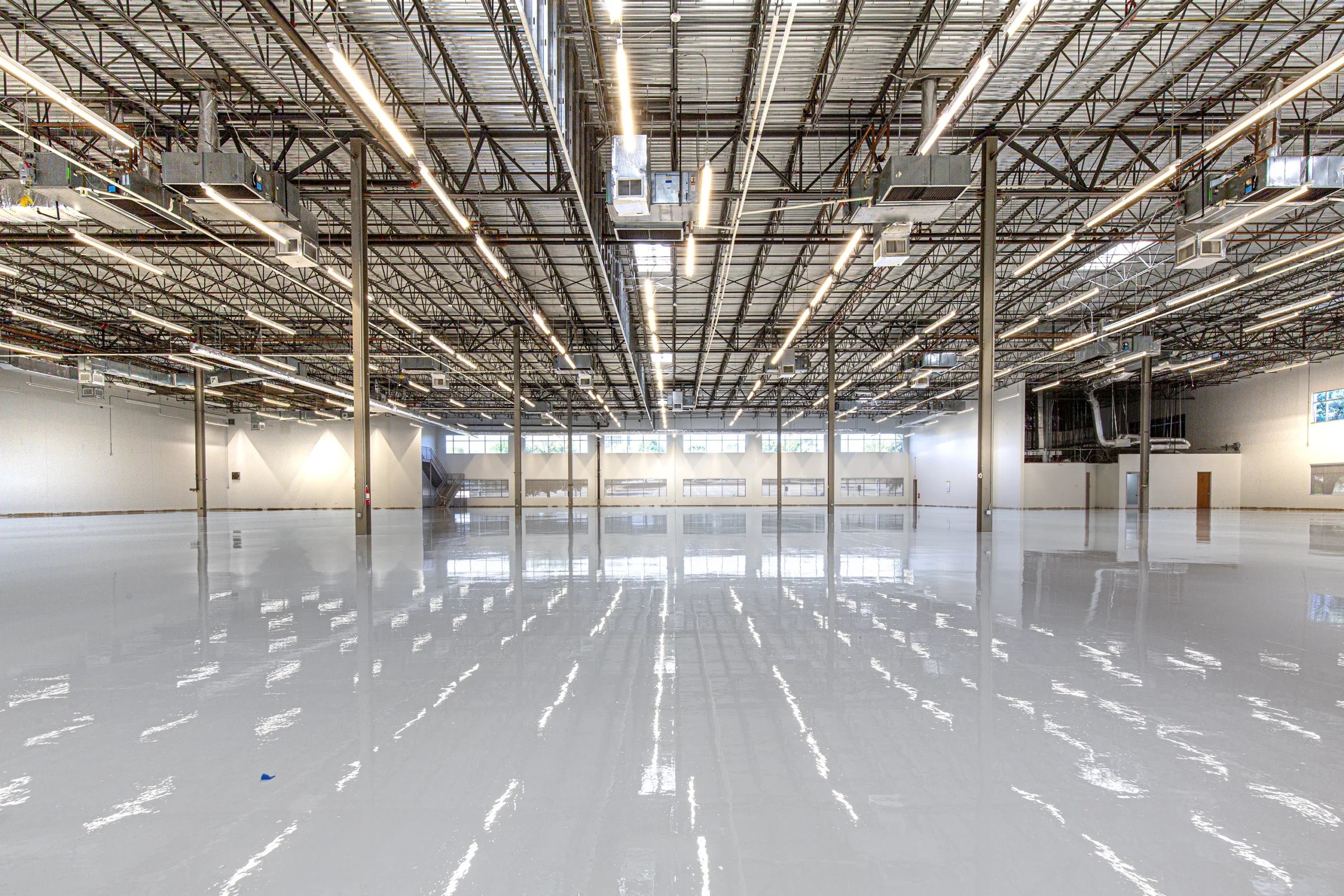
Other Aspects of Commercial Kitchen Design
health codes require commercial kitchens to have proper ventilation and exhaust systems. These systems must remove heat, humidity, smoke, and odors. Exhaust hoods must meet NFPA 96 standards. They also must be inspected and cleaned regularly. Proper ventilation helps maintain safe kitchen conditions and prevents buildup of harmful fumes, heat, and moisture.
Regulations require proper lighting in food prep areas, storage spaces, and dishwashing stations. Lighting must meet or exceed FDA Food Code standards. These rules specify lighting intensity such as 50 foot-candles at food preparation surfaces. Adequate lighting helps workers clearly see food conditions, cleanliness, and safety hazards, ensuring compliance with local health codes.
Meeting your city’s commercial kitchen flooring codes protects public health, prevents foodborne illness, and ensures worker safety, while avoiding citations, fines, or closures. Following proper flooring guidelines is essential to keep your kitchen compliant and your business running smoothly.
Epoxy Services We Offer
Recommended Commercial Kitchen Installation materials
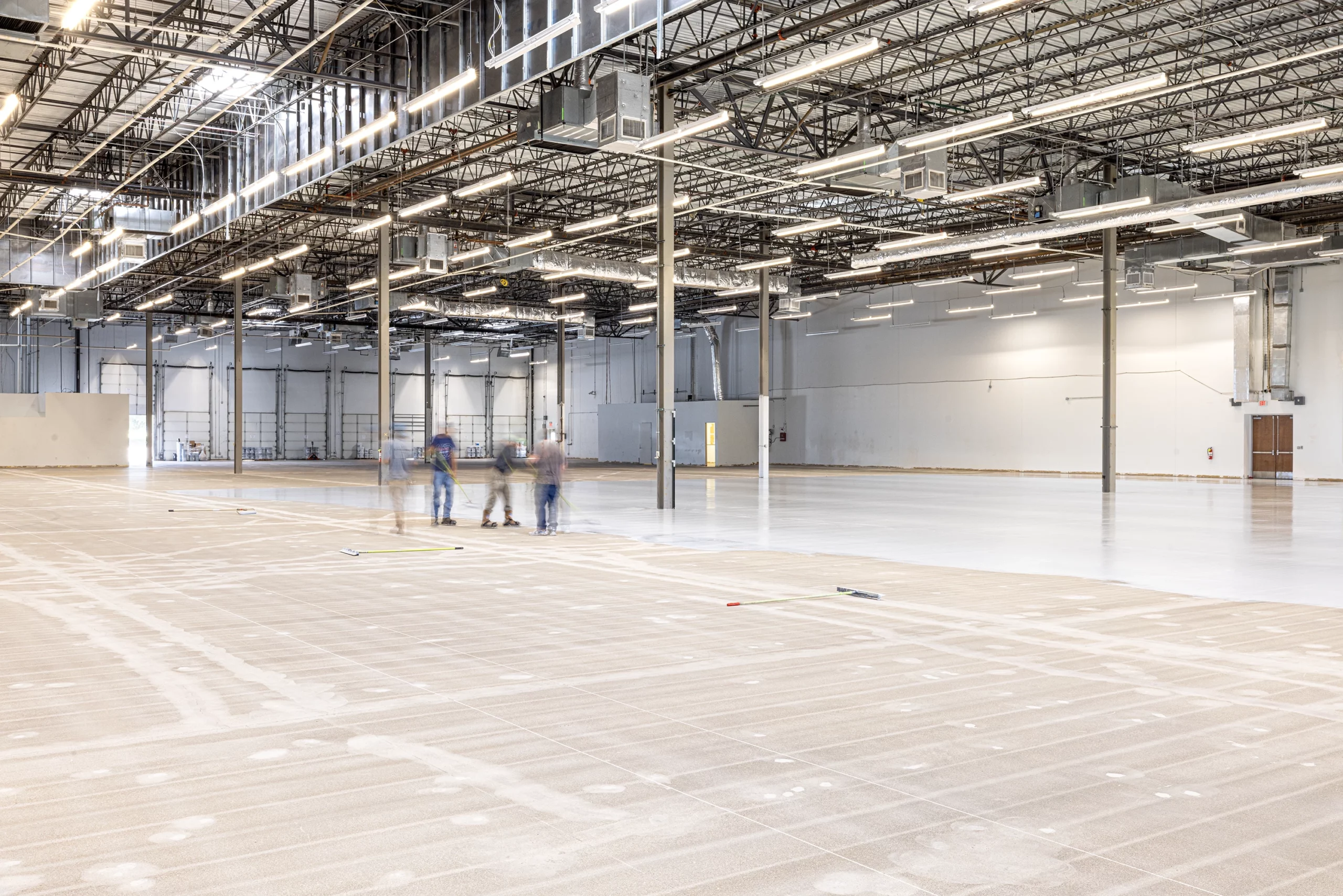
Urethane Cement Installation
According to health regulations, commercial kitchen flooring must be smooth, durable, and easy to clean, without cracks, open seams, or rough textures. Floors in food preparation areas, dishwashing stations, walk-in refrigeration units, and other wet zones must utilize nonabsorbent materials that resist moisture, grease, and food residue. Additionally, slip-resistant flooring is mandated to protect workers from slips and falls, even under wet or oily conditions. Urethane cement flooring effectively meets these stringent requirements, offering a seamless, durable, and moisture-resistant surface that prevents bacterial growth, ensures easy sanitation, and provides excellent slip resistance, thereby fully complying with modern health code standards.
Local health codes also require commercial kitchen floors to slope toward floor drains at a minimum rate of 1/8 inch per foot, preventing water accumulation and maintaining sanitary conditions. Additionally, coving at floor-wall junctures must be smooth, nonabsorbent, and feature a radius of at least 3/8 inch to facilitate cleaning and sanitation. Urethane cement flooring is particularly conducive to these specifications, as it can be precisely installed to achieve proper drainage slopes and seamlessly integrated coving, ensuring compliance with local health regulations and promoting hygienic kitchen environments.
Craftsman Concrete Floors specializes in installing and inspecting urethane cement flooring, ensuring full compliance with health regulations as well as USDA and FDA guidelines when applicable. Our in-house senior NACE Certified Inspector oversees each project, guaranteeing adherence to industry standards and local codes. With decades of combined expertise in installation, materials manufacturing, and product development, our skilled professionals deliver precise, high-quality urethane cement flooring solutions tailored to meet the specific needs of commercial kitchens.
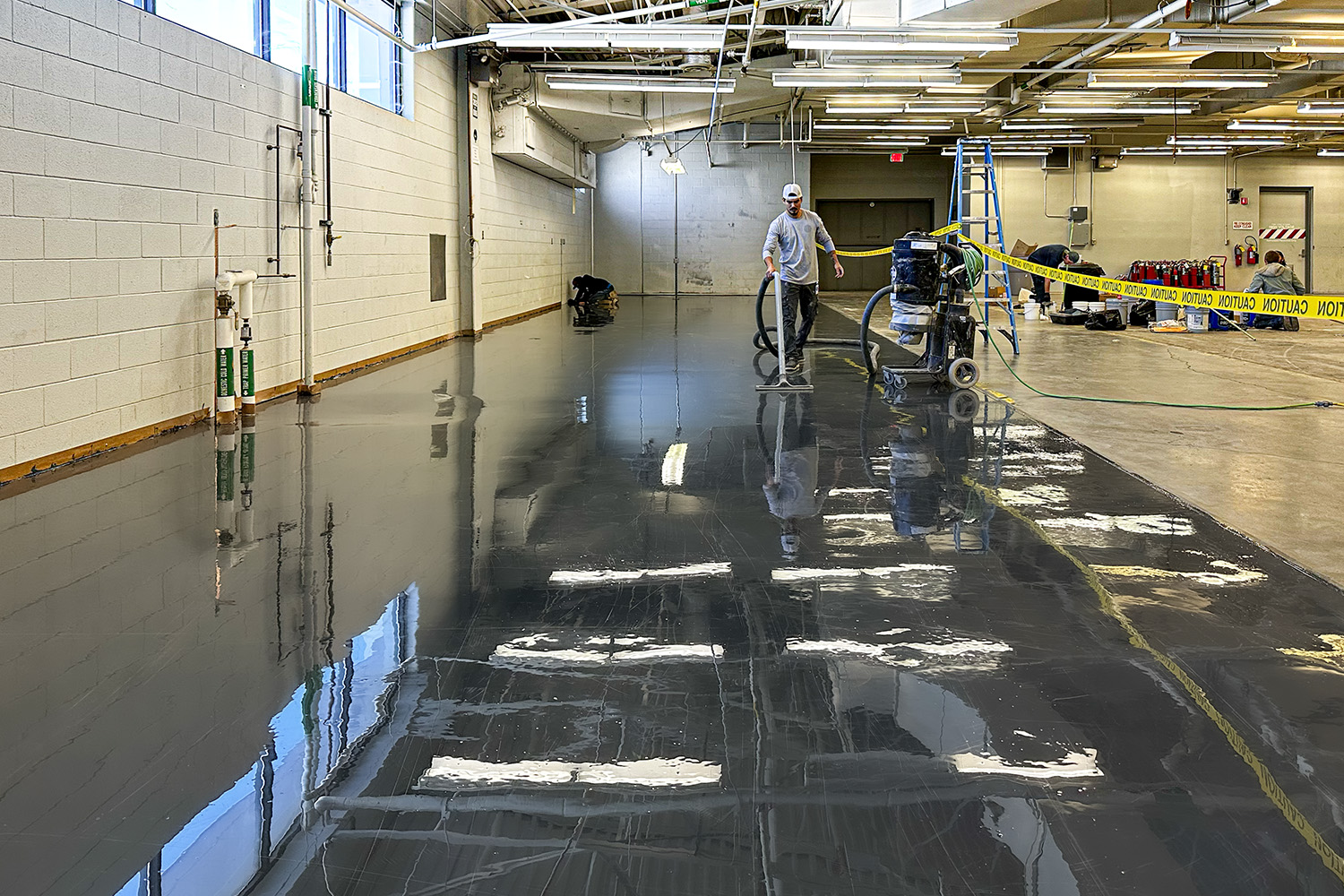
Double-Broadcast Epoxy Installation
Double broadcast epoxy flooring involves applying two layers of epoxy resin combined with broadcasted aggregate, creating a seamless, durable, and smooth surface. According to health regulations, commercial kitchen flooring must be smooth, durable, and easy to clean, without cracks, open seams, or rough textures. Double broadcast epoxy flooring effectively meets these requirements by providing a robust, seamless surface that prevents dirt accumulation and bacterial growth, ensuring compliance with local sanitation and safety standards.
Health codes mandate floor drains in food preparation, dishwashing, and frequently cleaned areas, requiring floors to slope toward drains at a minimum rate of 1/8 inch per foot. Unlike urethane cement, double broadcast epoxy flooring typically necessitates an additional sloping layer to achieve proper drainage compliance. However, epoxy systems are fully compatible with coved base junctures, meeting the required minimum 3/8-inch radius for smooth, nonabsorbent, and easily sanitized transitions between floors and walls.
Frequently Asked Questions about Urethane Cement Flooring
Urethane cement typically takes four hours to cure before any foot traffic is allowed on it, with full curing continuing for days afterwards. For maximum effectiveness, it is best to wait at least 12-18 hours before driving on freshly installed urethane cement.
Urethane cement is installed between 1/8″ and 1/4″ in thickness as a concrete topping and up to 6″ for concrete repairs.
Most urethane cement floor installations cost between $9 and $12 per square foot.
Blog
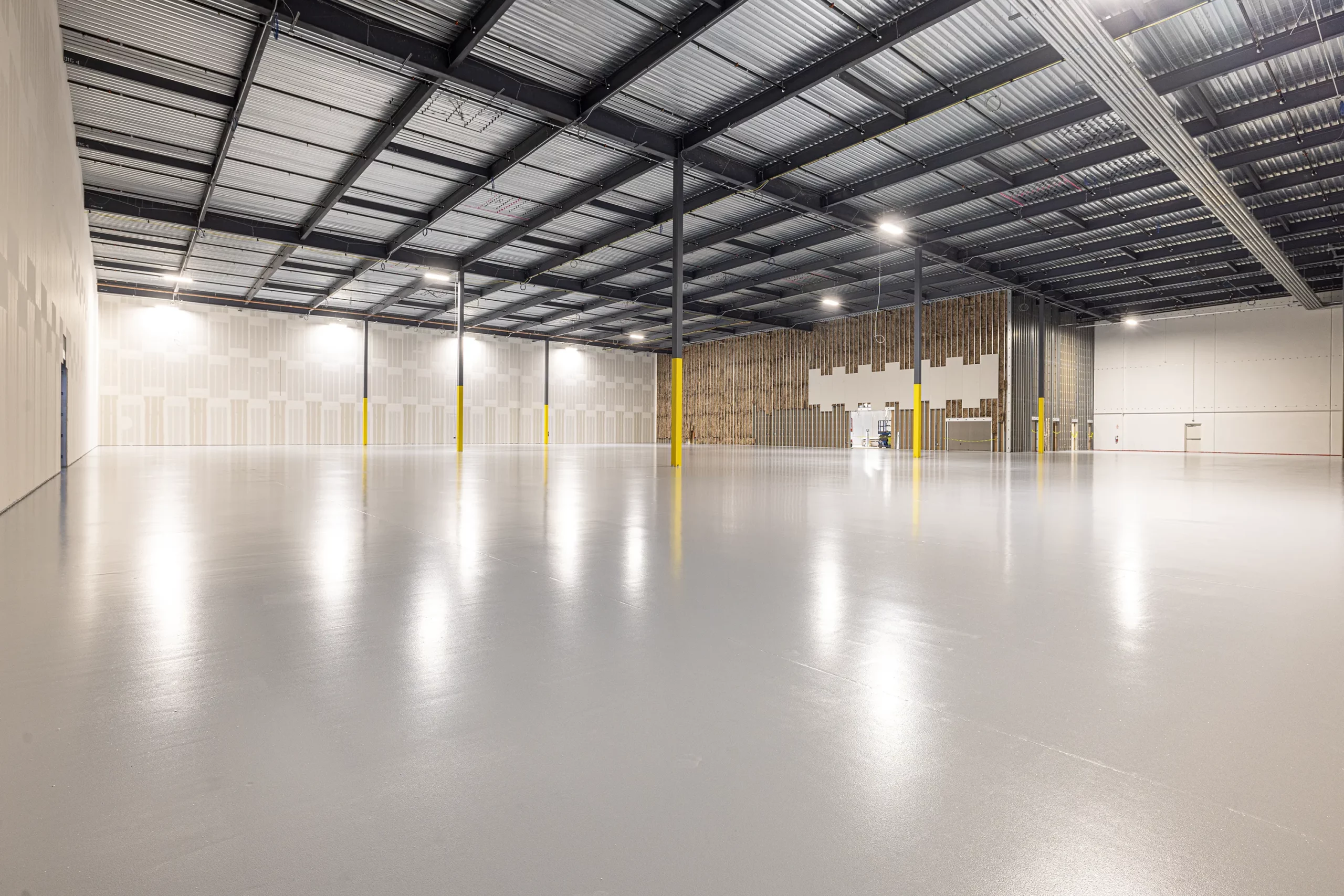
Project Highlight: 34,000 Sq. Ft. ESD Epoxy Installation in Dallas, Texas
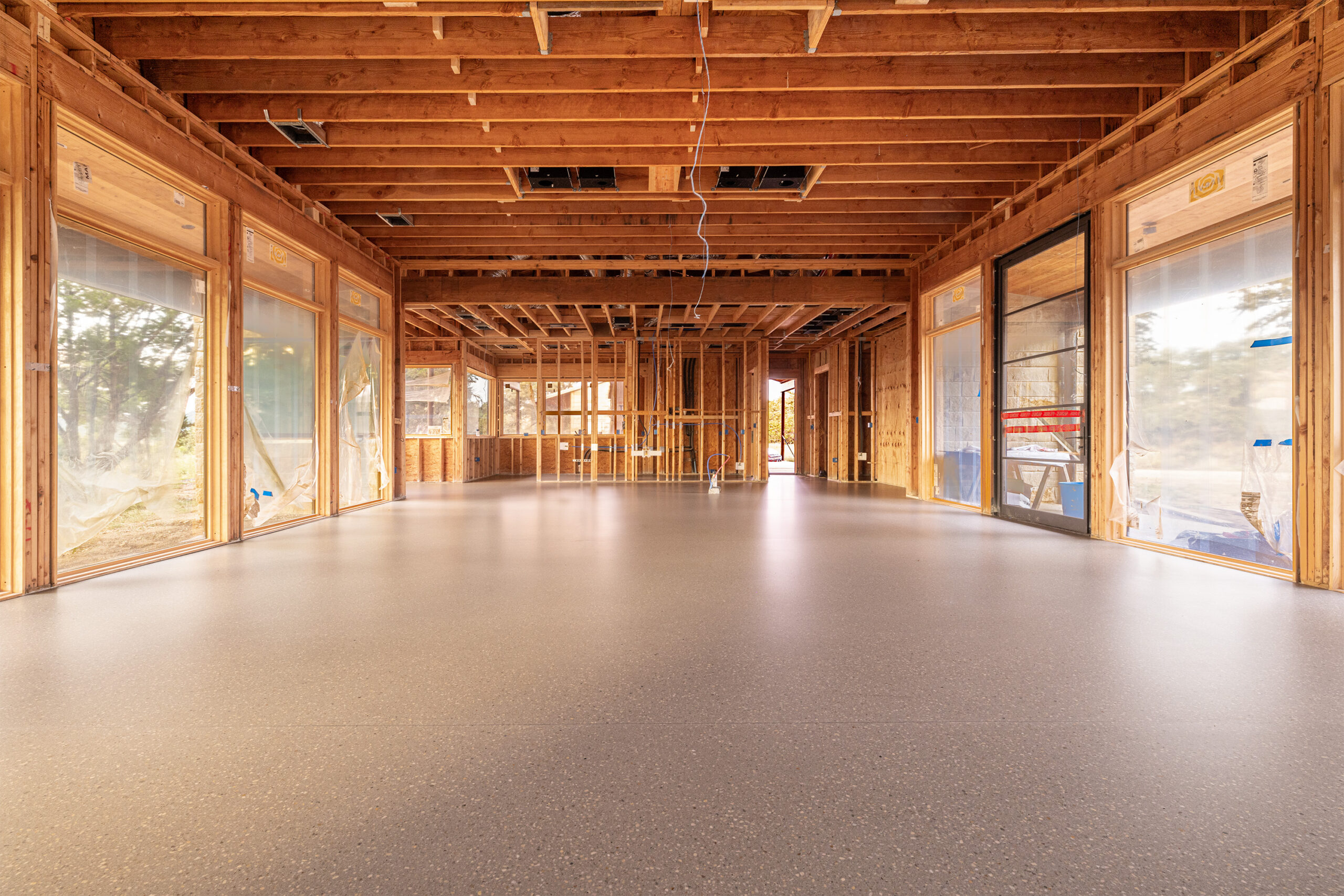
Project Highlight: New Residential Terrazzo Floors in Fort Worth, Texas
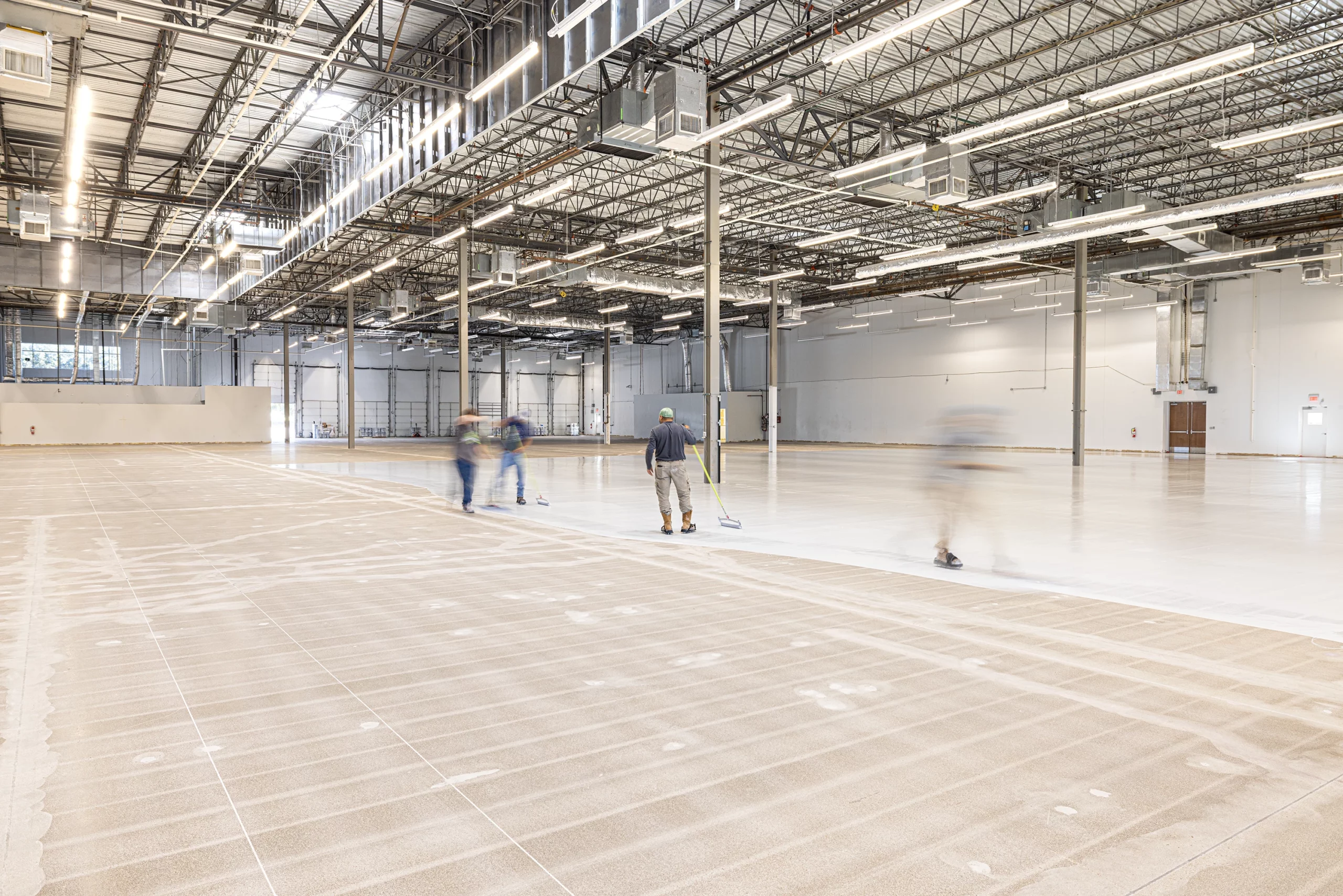