Epoxy Garage Floor Cost Guide
Craftsman Concrete Floors specializes in the installation of commercial-grade concrete coatings, including epoxy garage floors. These floors endure extreme conditions and require a long, uninterrupted service life. As one of the largest installers of specialized commercial concrete coatings in the nation, we have the expertise to provide coating systems that offer reliable, long-term concrete protection for builders and homeowners companies.
Are you planning to upgrade your garage? Transforming your plain, hard-to-clean concrete floor with an epoxy flooring system can significantly enhance its appearance and functionality. Epoxy garage floor systems are known for their durability, ease of cleaning and maintenance, and exceptional resistance to chemical spills.
In this article we will explore the costs associated with epoxy garage floors, highlighting the various price factors and the benefits of different epoxy systems.
Want to Learn More About Epoxy Floors?
We’re here to guide you through the design of our products. A Concrete Floor Specialist will reach out within one business day.
Average Prices for Epoxy Garage Floors
When it comes to installing a high-quality epoxy floor in a two-car garage, the typical cost ranges from $4,000 to $5,500. These epoxy garage floor systems utilize materials not readily available to homeowners, including 100% solids epoxy, polyurethane, and polyaspartic coatings. Known for their incredible durability, epoxy coatings are highly resistant to chemical spills from vehicle fluids and household cleaning products. Additionally, they are scratch and mar-resistant, ensuring they won’t transfer onto hot vehicle tires when a car is parked.
Labor Costs | $4 – $9 per sq. ft. | Varies on size and complexity |
Material Costs | $2 – $6 per sq. ft. | Varies on material quality and number of coats |
Standard Two-Car Garage Size | $4,000 – $7,000 | Total for 380 – 450 sq. ft. garage |
Solid Color Epoxy | $3 – $7 | Standard option, lower cost |
Factors That Impact Epoxy Garage Floor Cost
Various types of coatings are available for garage floors, each differing in quality and performance. Our standard epoxy garage floor system consists of a base layer of 100% solid epoxy, a full broadcast of plastic flakes, and a top layer of polyurethane or polyaspartic. Among the options listed below, our flake epoxy garage floor system is the preferred choice due to its superior durability and high slip resistance.
Water-based epoxy garage floors offer a more economical alternative to 100% solid epoxy floors and can often be installed by homeowners themselves. Big-box retailers like Lowe’s and Home Depot sell DIY kits that can be installed over a weekend. However, it’s important to recognize that these do-it-yourself epoxy systems do not provide the same level of chemical resistance and durability as professional-grade epoxy flooring systems. In our experience, DIY epoxy flooring typically lasts only one to two years before needing replacement.
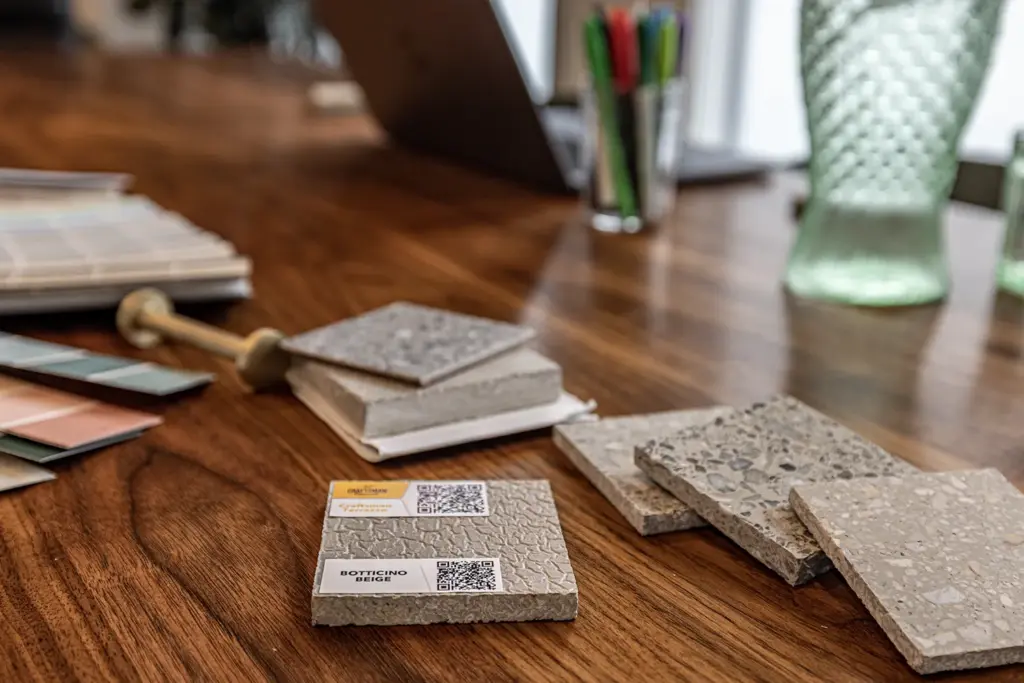
Garage Customization Options
Epoxy flooring offers a variety of customization options to meet both aesthetic preferences and functional requirements. Choices include metallic finishes, decorative flakes, and quartz broadcasts. While these options enhance the visual appeal of your epoxy garage floor, they also influence performance. For instance, flake and quartz broadcasted epoxy floors provide significantly greater slip resistance compared to metallic or solid-color epoxy floors. The following table summarizes the key options and their associated costs:
Price Range (sq. ft.) | Notes | |
Metallic Epoxy | $9 – $12 | Not recommended for garages |
Decorative Flakes | $7 – $10 | Provides slip resistance and aesthetics |
Quartz Broadcast | $9 – $12 | Offers excellent slip resistance and durability |
Solid Color Epoxy | $3 – $7 | Standard option, lower cost |
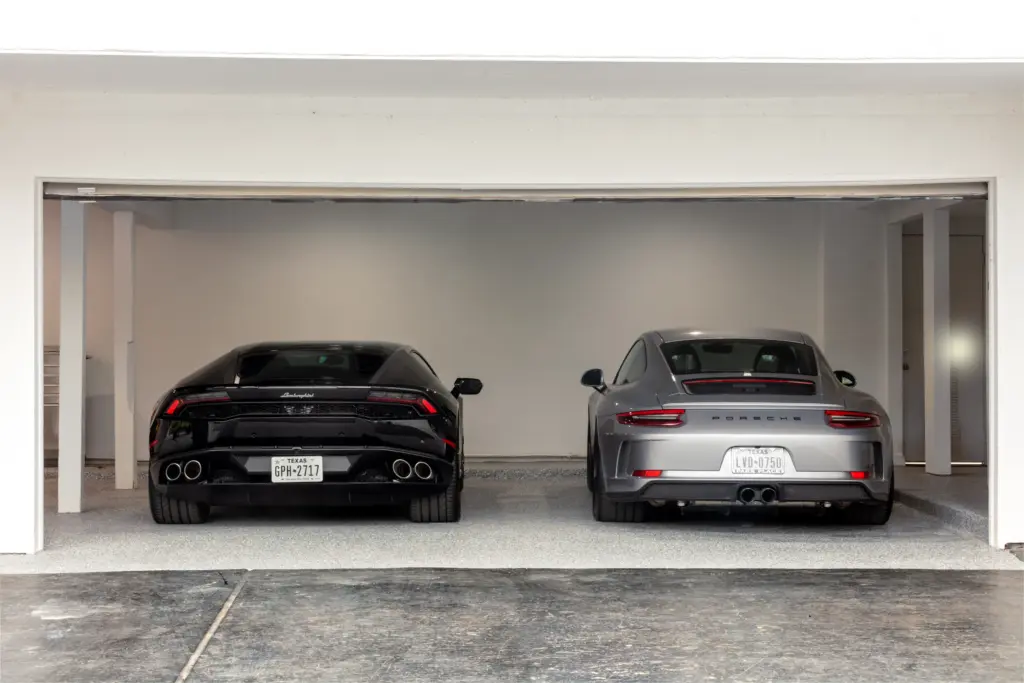
Size of the Garage Floor
The size of the garage floor is a key factor influencing the cost of epoxy flooring. Generally, larger areas tend to have a lower cost per square foot. For example, a two-car garage covering approximately 400 square feet may incur a cost of around $4,000, while a larger project spanning 1,000 square feet could cost about $8,000.
This cost efficiency arises because many fixed expenses associated with the installation—such as labor and equipment—can be distributed over a larger area, effectively lowering the overall cost per square foot. Additionally, for larger projects, material costs can decrease as supplies are often purchased in bulk, further enhancing savings.
Cost Comparison Table
Garage Size | Approximate Cost |
400 sq. ft. (Two-Car Garage) | $5,000 |
1,000 sq. ft. | $8,000 |
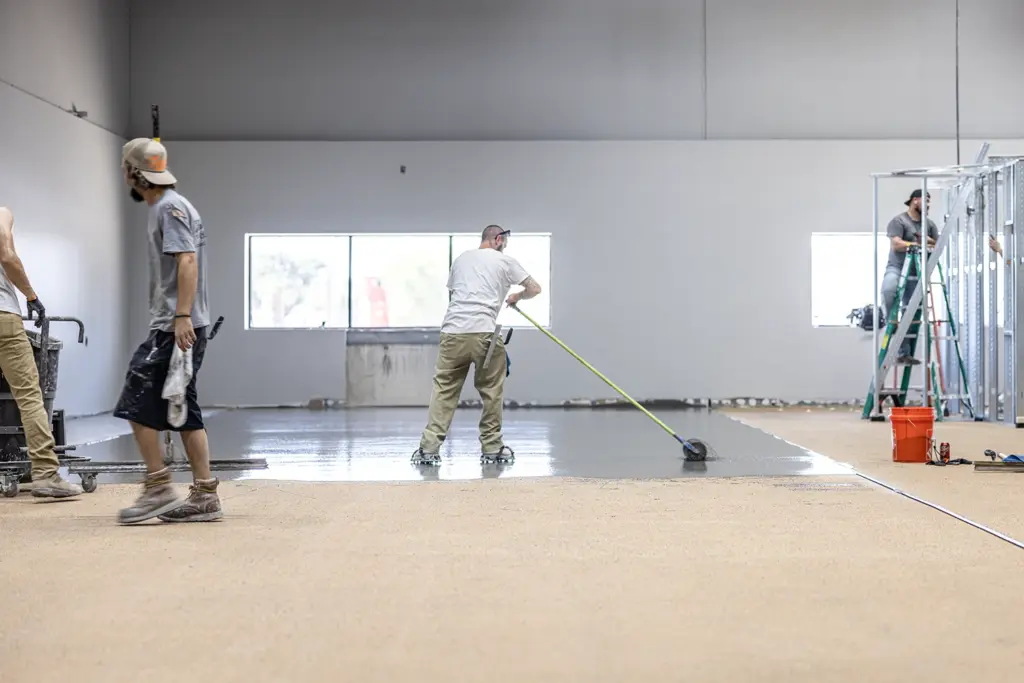
Labor Costs
Labor costs play a crucial role in determining the overall expenses associated with epoxy flooring installation, typically ranging from $5 to $15 per square foot in Texas. These costs can fluctuate based on factors such as location and the complexity of the project.
While attempting a DIY epoxy flooring installation may seem like a way to save on labor costs, it requires considerable effort, expertise, and the right tools and equipment. If you’re uncertain about your capability to complete the project successfully, it’s advisable to hire a professional. This ensures not only a smoother installation process but also a high-quality finish that meets industry standards
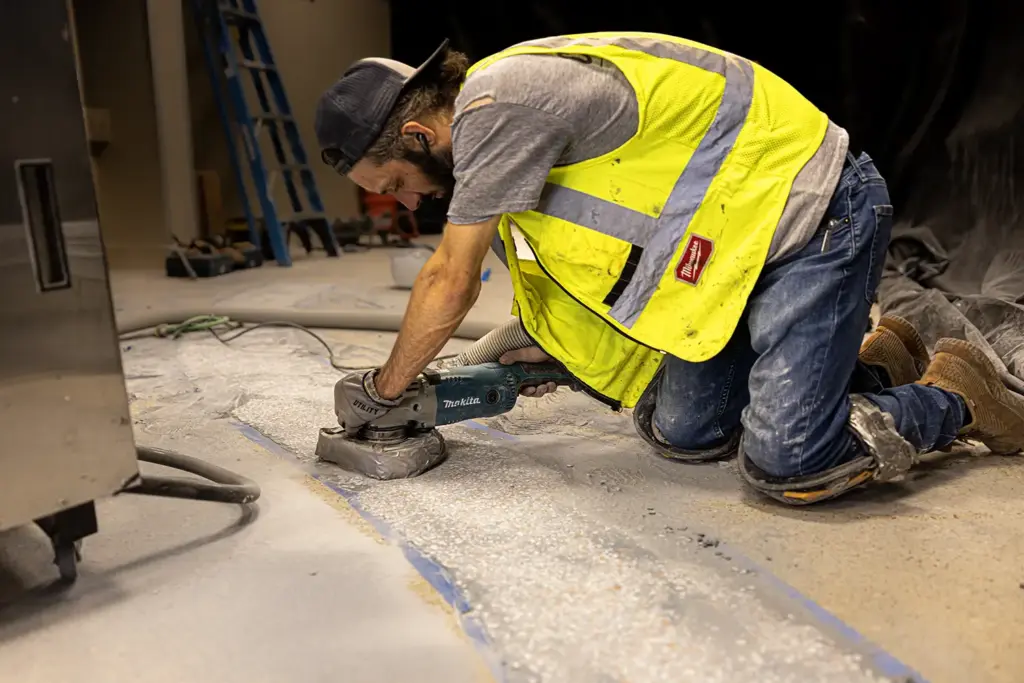
Thoughts on One-Day Polyaspartic Floors
While one-day polyaspartic floors might seem attractive because of their lower price, their durability is compromised due to the fast-curing material that does not adhere as effectively to the concrete. This can lead to issues such as peeling or chipping over time.
At Craftsman Concrete Floors, we never use a full polyaspartic system because they simply do not meet our standards for quality and longevity. We prioritize materials that ensure a long-lasting and resilient flooring solution, offering better performance and value for our customers.
Our Clients
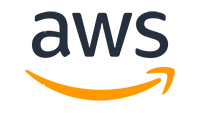
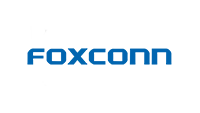
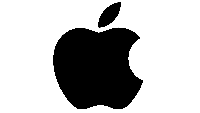
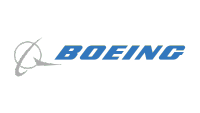
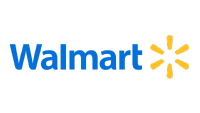
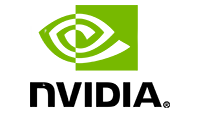
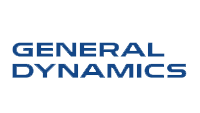
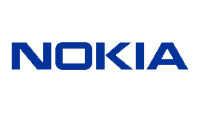
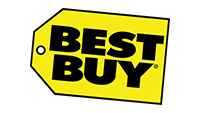
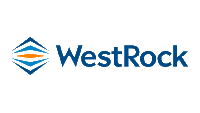
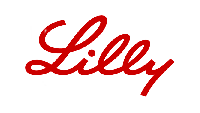

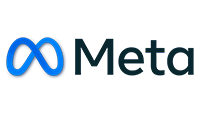
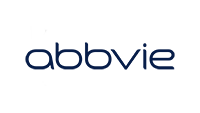
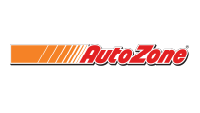
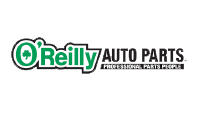
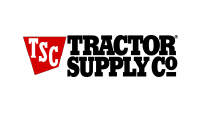
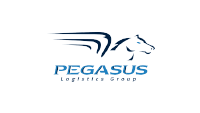
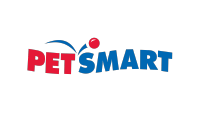
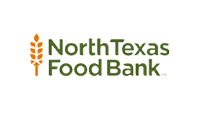
Epoxy Services We Offer
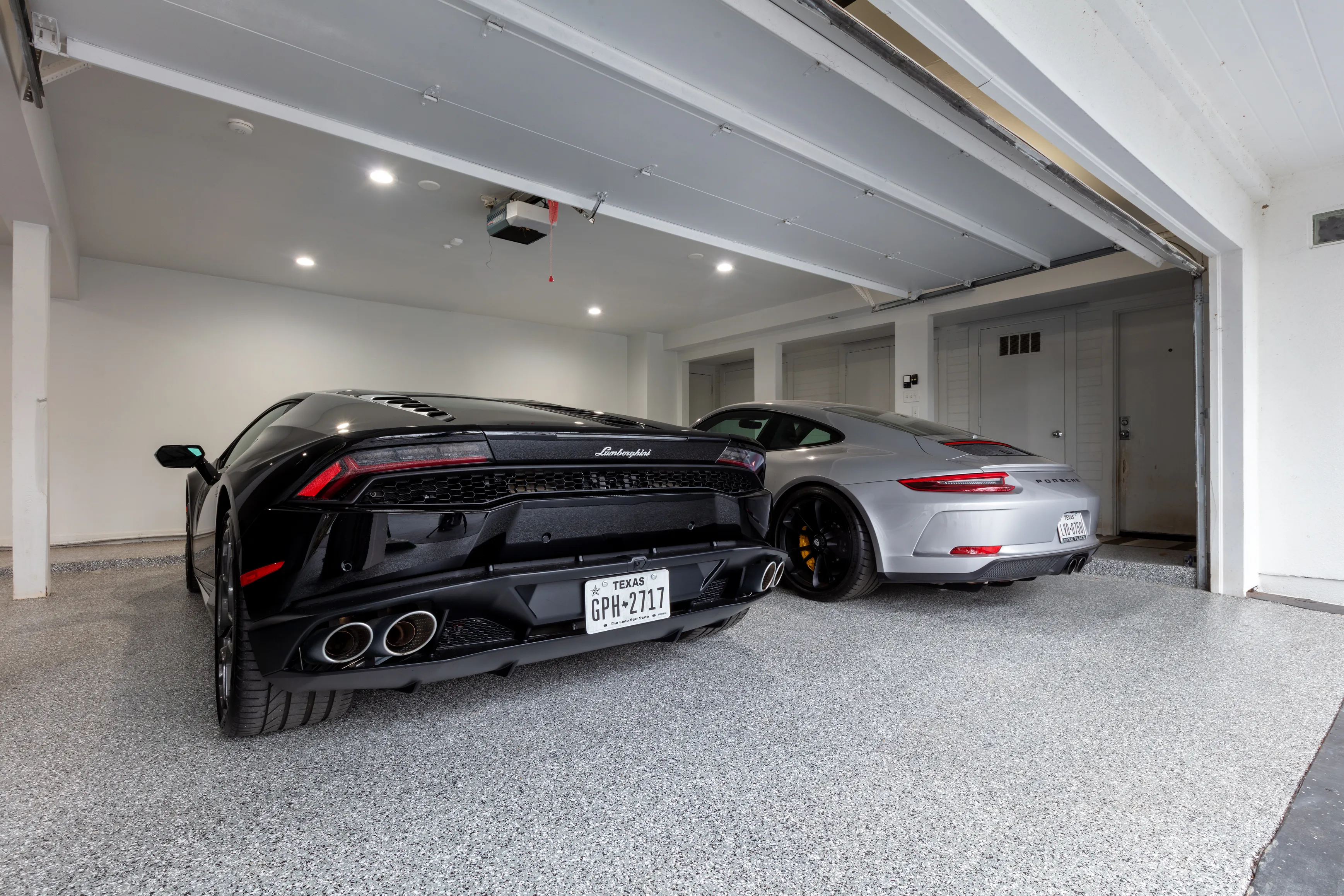
Comparing Epoxy Flooring Prices
Now that we’ve explored the various factors that can affect the cost of epoxy flooring, it’s time to compare the prices of different types of epoxy flooring systems. This section will examine the costs of solid-color epoxy floors, metallic epoxy floors, urethane floors, and urethane cement flooring.
By comparing the costs and benefits of each option, you can make an informed decision about which type of epoxy flooring best suits your needs and budget.
Solid-Color Epoxy Floors
Solid-color epoxy flooring consists of one or more layers of epoxy without slip additives like plastic flakes or quartz sand. Although we do not recommend these systems for garage floors due to their slippery nature when wet and tendency to show wear easily, they are popular in various applications, including manufacturing and storage facilities.
- Cost: Approximately $2 per square foot for materials, plus an additional $2 to $4 per square foot for installation labor.
While solid epoxy flooring may lack the aesthetic customization options of more expensive choices like metallic epoxy, they provide an excellent balance of performance and affordability for certain use cases. Keep in mind that we do not recommend this installation for residential garages due to slipperiness.
Metallic Epoxy Floors
Metallic epoxy floors offer an eye-catching appearance that sets them apart from standard epoxy flooring options. By incorporating metallic pigments into the epoxy coating, these floors create a stunning, shimmering finish that can be customized to suit your design preferences.
- Cost: Ranges from $9 to $12 per square foot.
Despite their higher price tag, the aesthetic appeal and customization options of metallic epoxy can justify the investment for those looking to create a unique flooring solution. Moreover, metallic epoxy floors maintain the same durability and resistance to wear as standard epoxy floors.
Urethane Floors
Polyurethane garage floors are a popular alternative to epoxy floors, particularly because they are not UV-reactive and therefore do not yellow when exposed to sunlight. Urethane systems can be installed on outdoor surfaces like sidewalks, driveways, and pool decks, often incorporating pebbles or river rocks for a textured appearance.
- Cost: Ranges from $8 to $20 per square foot.
While urethane floors may be more expensive, their performance on exterior surfaces can make them an appealing option for certain applications.
Urethane Cement
Urethane cement is commonly used in breweries and manufacturing facilities. This flooring solution combines epoxy and cement to create a surface that is more durable than either material alone. It provides exceptional resistance to mechanical abrasion, harsh chemicals, thermal shock, and impact damage, making it ideal for garages that experience heavy use.
- Cost: Typically exceeds $20 per square foot for average garage installations.
While urethane cement floors can be costly, their high durability and performance in demanding environments make them a solid choice for industrial settings.
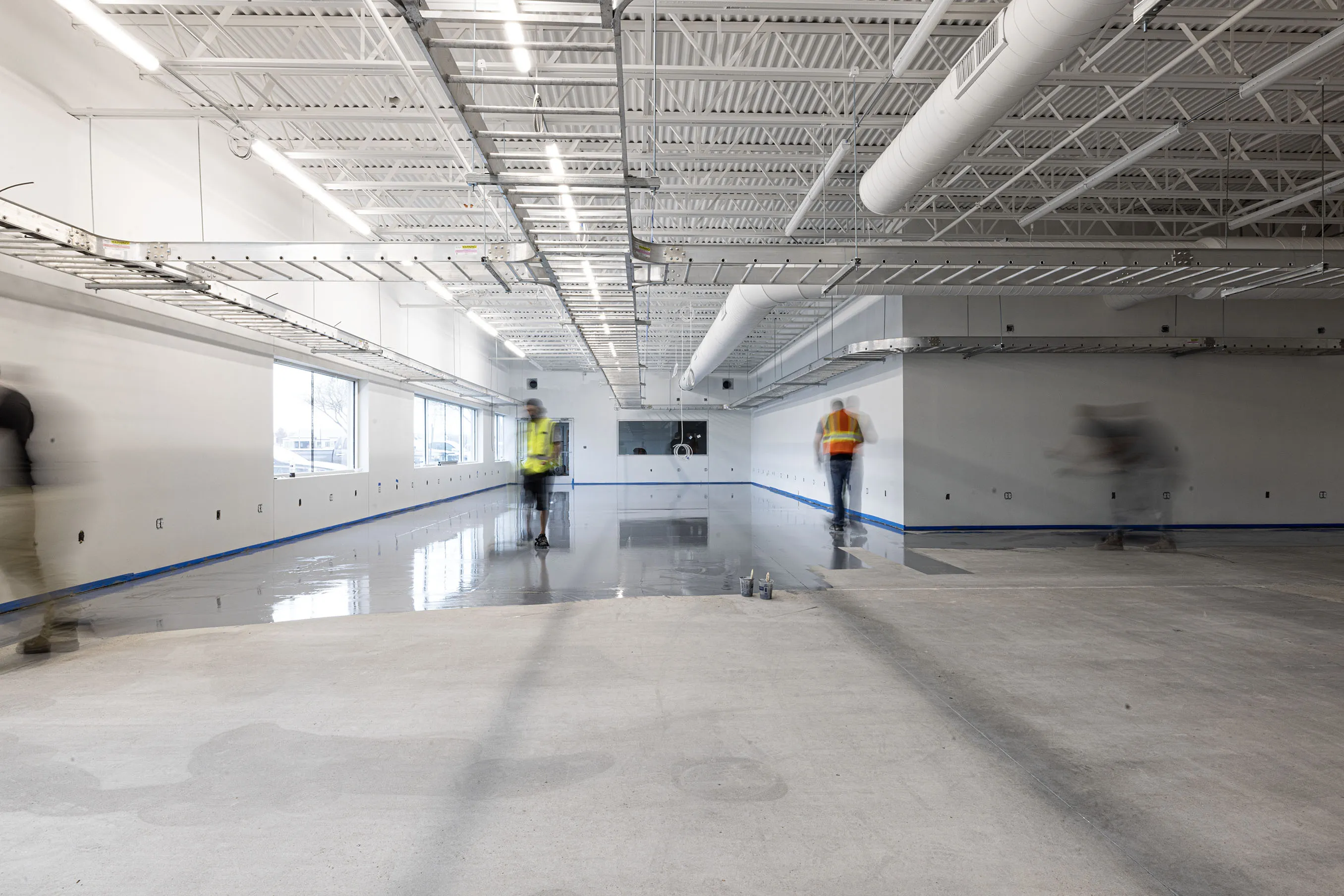
Other Epoxy Garage Floor Costs
Concrete Repairs
For an epoxy coating to be effective and durable, any damage to the concrete slab must be repaired prior to installation. Cracks and spalling damage are typically addressed with specialized fast-cure epoxy. Before starting the epoxy flooring project, the installation company should assess any necessary repairs. In rare cases, significant deterioration of the concrete slab may render the epoxy coating project unfeasible. At Craftsman Concrete, we charge a flat rate for slab repairs, which usually ranges from $250 to $750 per project.
Moisture Testing
Moisture testing is a critical step in the epoxy flooring installation process, as epoxy cannot be applied to a concrete slab that contains moisture. This testing ensures that the concrete is sufficiently dry to accept the epoxy; excess moisture can prevent proper adhesion, leading to cracking and peeling.
The cost of moisture testing typically ranges from $200 to $500. While this may seem like a considerable expense, it’s essential to recognize the potential long-term costs of applying epoxy to a damp concrete floor. Investing in moisture testing is crucial to preventing future issues and ensuring a successful epoxy flooring installation.
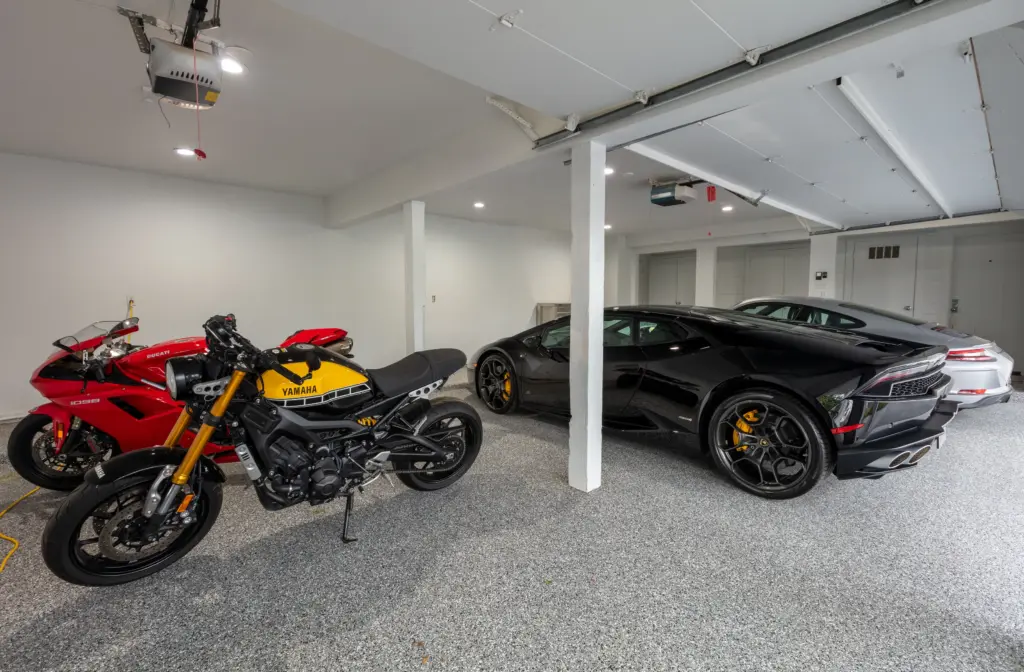
Frequently asked Questions
Epoxy garage flooring is highly durable and designed to resist impacts from dropped tools and equipment. However, extremely sharp or heavy objects can occasionally cause minor chips or dents. Regular care and immediate attention to any significant impacts will help maintain the floor’s integrity throughout its expected 10-year lifespan.
Yes, epoxy garage floors are resistant to most common automotive fluids, including motor oil, antifreeze, and brake fluid. These substances can be quickly and easily wiped up without staining or damaging the epoxy coating. Promptly cleaning spills ensures the coating stays pristine and maintains its protective qualities.
Epoxy garage floors perform well in cold climates and can withstand repeated freeze-thaw cycles without cracking or deterioration. Proper preparation of the concrete surface and using high-quality epoxy materials are crucial to ensure long-term durability in colder environments. With correct installation, epoxy flooring remains stable and functional through temperature fluctuations for its expected lifespan.
we install Esd epoxy floors nationwide, including:
Albuquerque, NM; Albany, NY; Anaheim, CA; Anchorage, AK; Arlington, TX; Arlington, VA; Atlanta, GA; Austin, TX; Bakersfield, CA; Baltimore, MD; Baton Rouge, LA; Birmingham, AL; Boise, ID; Boston, MA; Buffalo, NY; Chandler, AZ; Charleston, SC; Charlotte, NC; Chicago, IL; Chula Vista, CA; Cincinnati, OH; Cleveland, OH; Colorado Springs, CO; Columbus, OH; Corpus Christi, TX; Dallas, TX; Dallas-Fort Worth, TX; Denver, CO; Detroit, MI; Durham, NC; El Paso, TX; Fort Worth, TX; Fremont, CA; Fresno, CA; Garland, TX; Gilbert, AZ; Glendale, AZ; Grand Rapids, MI; Greensboro, NC; Hartford, CT; Hialeah, FL; Honolulu, HI; Houston, TX; Huntsville, AL; Indianapolis, IN; Irvine, CA; Jacksonville, FL; Jersey City, NJ; Kansas City, MO; Las Vegas, NV; Laredo, TX; Lexington, KY; Lincoln, NE; Long Beach, CA; Los Angeles, CA; Louisville, KY; Lubbock, TX; Madison, WI; Memphis, TN; Mesa, AZ; Miami, FL; Milwaukee, WI; Minneapolis, MN; Nashville, TN; New Orleans, LA; Newark, NJ; Norfolk, VA; North Las Vegas, NV; Oakland, CA; Oklahoma City, OK; Omaha, NE; Orlando, FL; Philadelphia, PA; Phoenix, AZ; Pittsburgh, PA; Plano, TX; Portland, OR; Providence, RI; Raleigh, NC; Reno, NV; Richmond, VA; Riverside, CA; Sacramento, CA; Salt Lake City, UT; San Antonio, TX; San Diego, CA; San Francisco, CA; San Jose, CA; Santa Ana, CA; Scottsdale, AZ; Seattle, WA; Spokane, WA; St. Louis, MO; Stockton, CA; Tampa, FL; Toledo, OH; Tucson, AZ; Tulsa, OK; Virginia Beach, VA; Washington, DC; Wichita, KS; Winston–Salem, NC
Blog

Project Highlight: 34,000 Sq. Ft. ESD Epoxy Installation in Dallas, Texas
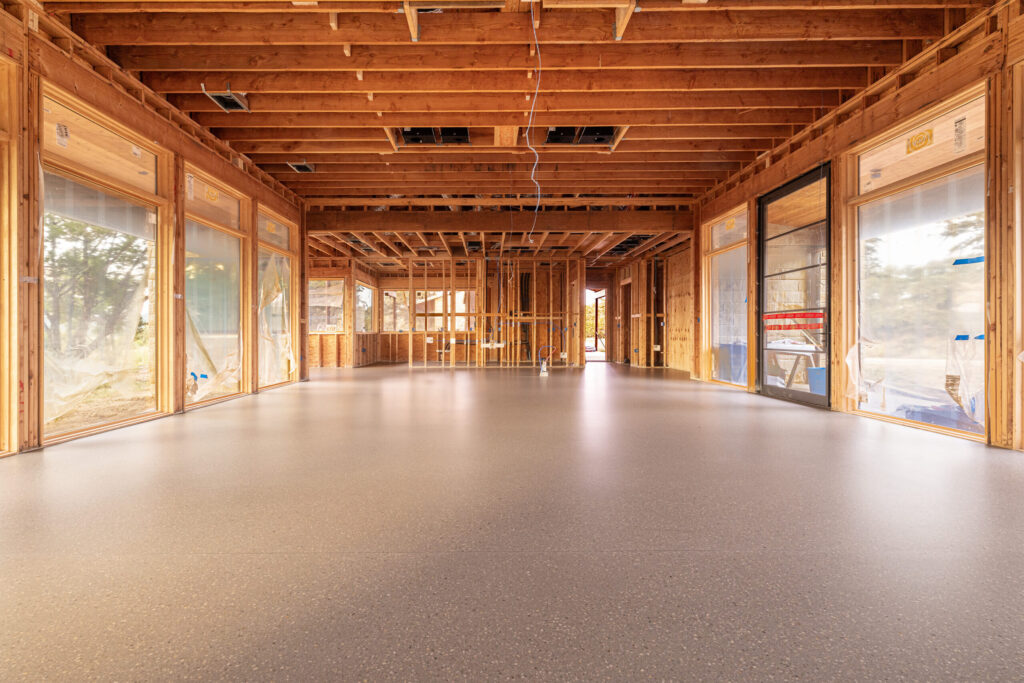
Project Highlight: New Residential Terrazzo Floors in Fort Worth, Texas
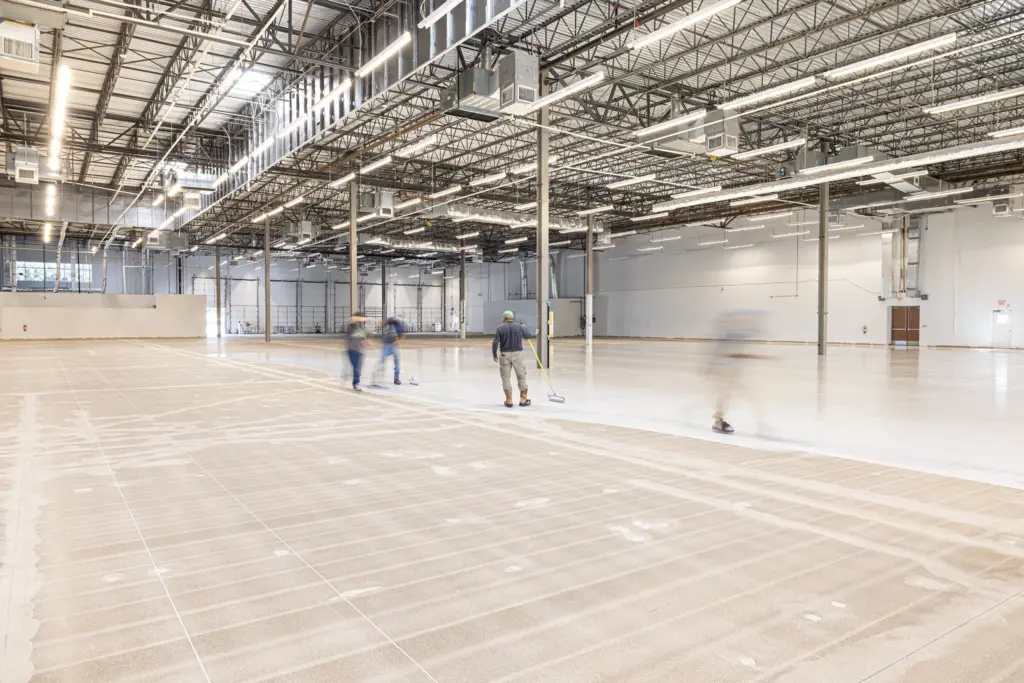