Builders Guide to Polished Concrete Floors
Installing concrete floors in a new construction project can increase profitability, reduce construction time and complexity, and shorten time on market. However, understanding the key aspects of installation is crucial for a successful outcome. From proper slab preparation to finishing techniques, careful planning can ensure a durable and visually appealing result.
At Craftsman Concrete Floors, our commitment is to environmental sustainability. We know that our customers install concrete flooring to minimize waste and environmental impact. To support this commitment, we power our facilities with 100% renewable energy, use electric cars where possible, and purchase carbon credits to offset the greenhouse gases from our other vehicles.
Want to Learn More about Concrete Floors?
We’re here to guide you through the design of our products. A Concrete Floor Specialist will reach out within one business day.
How to Install Polished Concrete Floors in a House
Installing a Polished Concrete Floor is a time-sensitive process that requires an experienced contractor to get optimum results. Here are the primary factors that establish an installation guide and how you can estimate the project’s completion date.
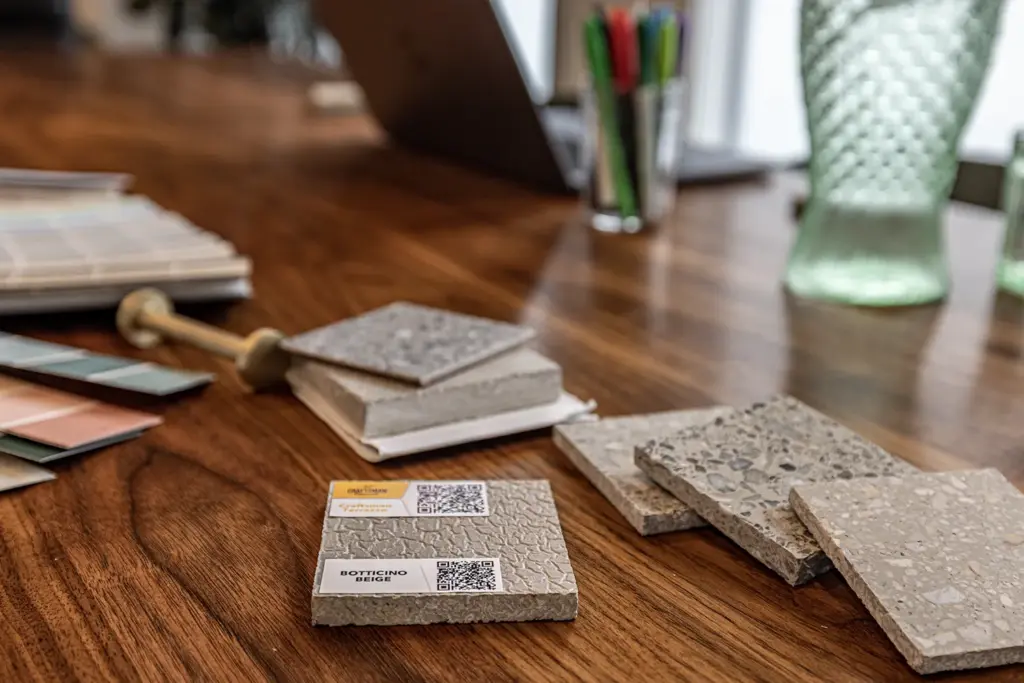
Types of Polished Concrete Floors
The choice of polished concrete flooring for a new residential project can significantly impact steps, costs, and timelines. The pricing below is based on individual projects of 1,500 sq. ft. or larger. Note that higher volume builds (e.g., adjacent single-family homes, apartment buildings, or track homes) may be priced lower. This type of polished concrete is especially well-suited for new residential construction, where it is one of the most common installations.
Cream Polished Concrete
Most commonly selected by builders due to its incredible value and performance.
- Achieved by polishing the unground surface of a newly poured concrete slab
- Standard option for volume builders
Price Range: $3.00 – $5.00 per square foot
Salt and Pepper Polished Concrete
Popular choice for higher-end luxury or custom homes due to its consistent texture.
- Surface is lightly ground before polishing
- Removes power trowel markings and exposes small, colorful sand aggregates
- More durable than cream-polished concrete, ideal for high-traffic homes
Price Range: $4.50 – $7.00 per square foot
Rock Cut Polished Concrete Floor
The ultimate choice for luxury residential projects, offering a striking, timeless texture.
- Installed by heavily grinding the concrete surface before polishing
- Creates a look similar to terrazzo flooring
Starting Price: $9.00 per square foot
Visit Our Styles of Polished Concrete Floors Page for More Options
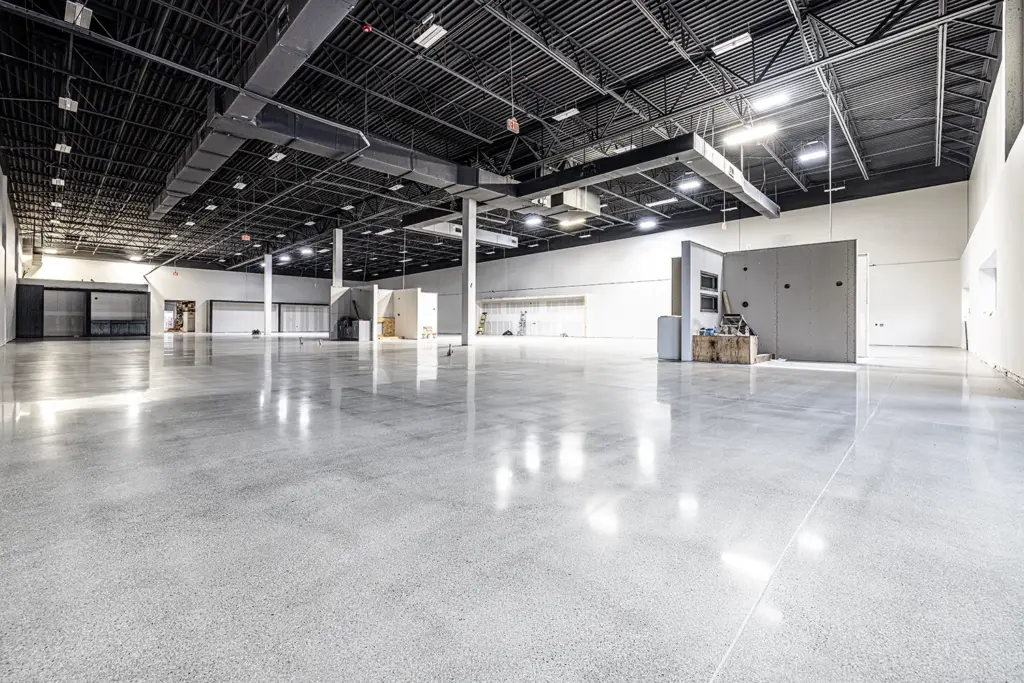
Polished Concrete Gloss Levels
“Polished concrete” refers to a floor that is honed to a smooth finish, rather than the level of reflectivity. The reflectivity of the surface is determined by the number of abrasive steps used during the polishing process. More abrasive steps result in a higher gloss level. The three primary gloss levels are satin, offering the lowest reflectivity; semi-gloss, with a medium shine; and high-gloss, which delivers the highest level of reflectivity.
Gloss levels for polished concrete can range from satin to high gloss, with minimal impact on pricing. While there’s no strict rule, matte finishes are commonly chosen for modern construction designs, whereas high-gloss floors are often used to enhance light and create a sense of openness in darker or more confined spaces. No matter the gloss level you select, all of our floors deliver the same high standard of quality and performance.
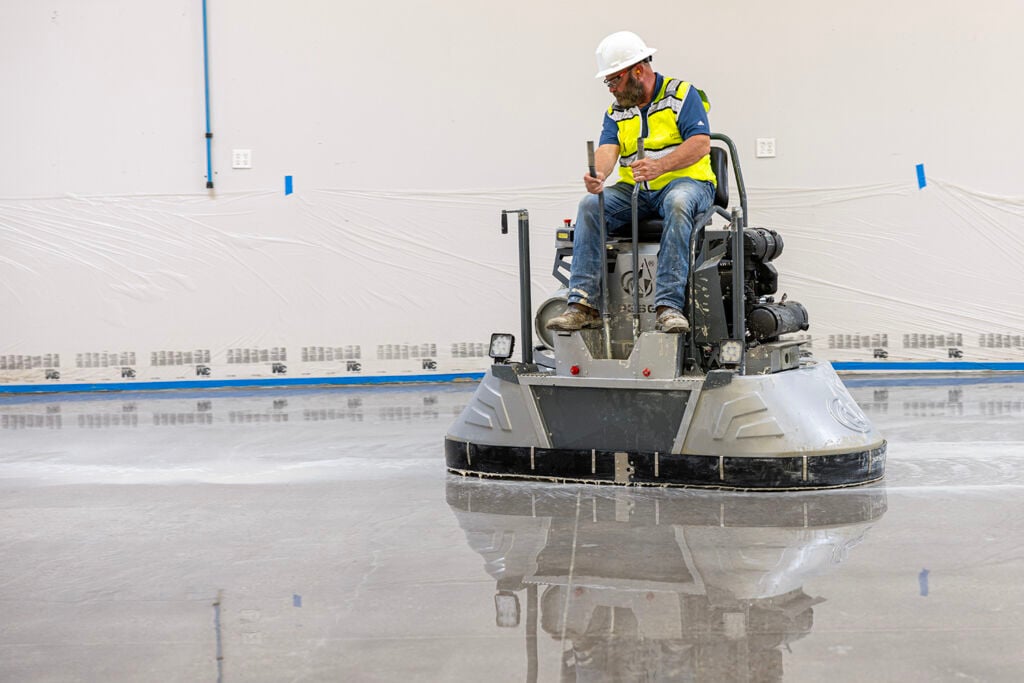
Concrete Pour and Troweling Technique
One of the most common questions we receive from home builders is about best practices for concrete pours, as the quality of the pour directly affects the final appearance of polished concrete floors. While almost any concrete can be polished, achieving the best results relies heavily on a well-executed pour.
Here are some key best practices:
Avoid using ‘cure and seal’ compounds. These offer no benefit for concrete that will be polished and will only increase the cost of installation.
Install anchor bolts after the pour to allow a power trowel to run along the edge of the slab. Hand-troweled areas tend to have a less consistent appearance than those finished with a power trowel.
Avoid overworking the concrete to prevent creating dark areas that cannot be reversed during polishing. To limit friction and prevent surface “burning,” use plastic float pans under the power trowel before switching to steel blades. Plastic blades are also a great alternative for keeping the slab light in color. While you can darken a slab later with pigment, it’s impossible to lighten one that has been burned.
Do not leave materials on a freshly poured slab. Objects left on the slab during curing can leave ghost marks, which will be visible once the concrete is polished.
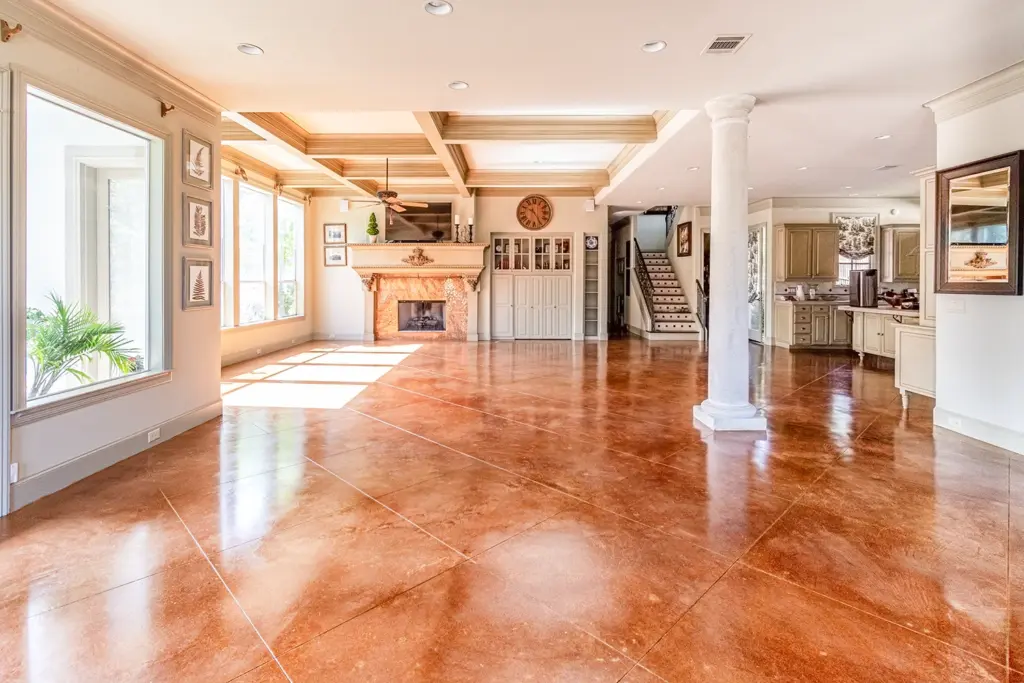
Stained Vs. Polished Concrete Floors
While the terms “stained” and “polished” concrete are often confused, polished concrete is generally the better option for residential construction. Polished concrete floors rely on penetrating treatments that enhance durability and stain resistance, while stained concrete floors use a film-forming plastic coating on the surface. In practice, this means that the wear surface of a polished concrete floor is the concrete itself—an extremely durable material. In contrast, the wear surface of a stained concrete floor is a softer plastic coating, which is more prone to scratching and visible wear.
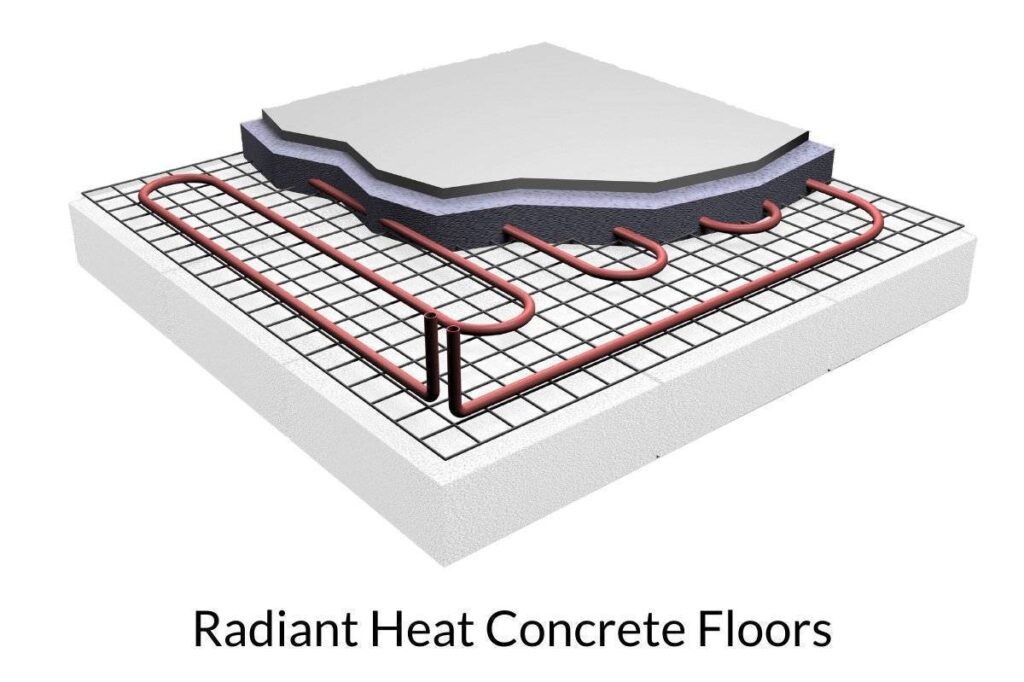
Radiant Heating in Polished Concrete
In-floor heating can be added to a polished concrete floor, but it must be coordinated with a radiant heating specialist before the slab is poured. Since concrete floors can be several degrees cooler than the ambient interior temperature during winter, installing in-floor heating can significantly improve comfort. Additionally, radiant heating is more efficient than traditional forced-air systems, which can lead to lower utility costs and enhanced sustainability.
Learn more about the benefits of radiant heating
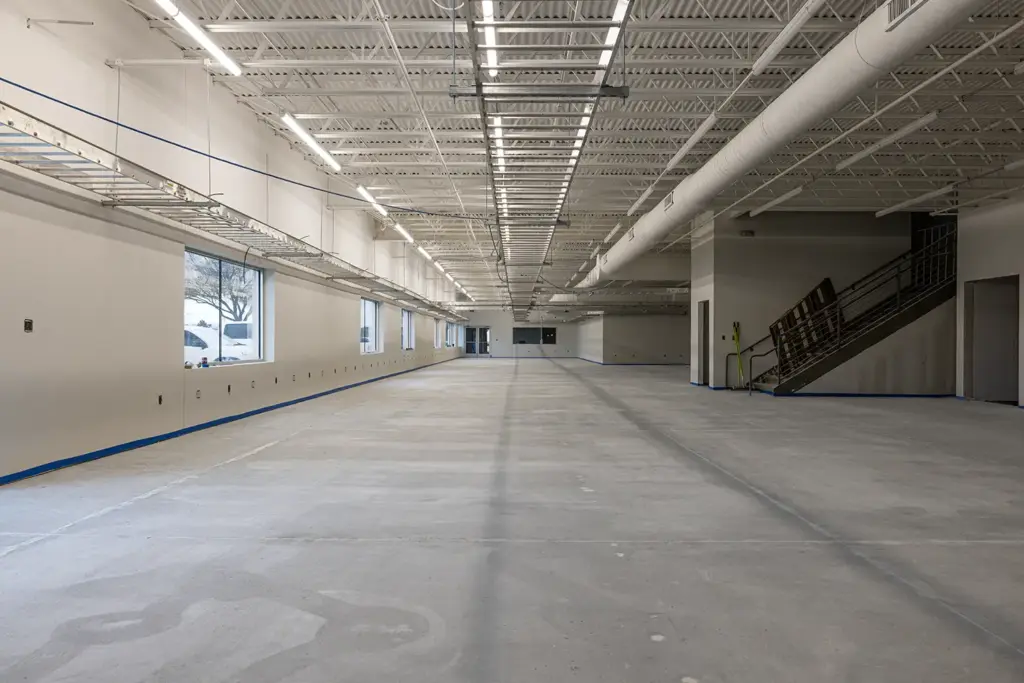
Commercial Polished Concrete Floors
Concrete polishing is a preferred flooring option in high-traffic areas, including:
- Warehouses
- Grocery stores
- Industrial spaces
- Hotels
- Offices
- Schools
Cost per square foot depends on various factors and typically decreases for larger projects due to economies of scale, while smaller projects often have higher costs per unit area.
Learn More About Polished Concrete Pricing
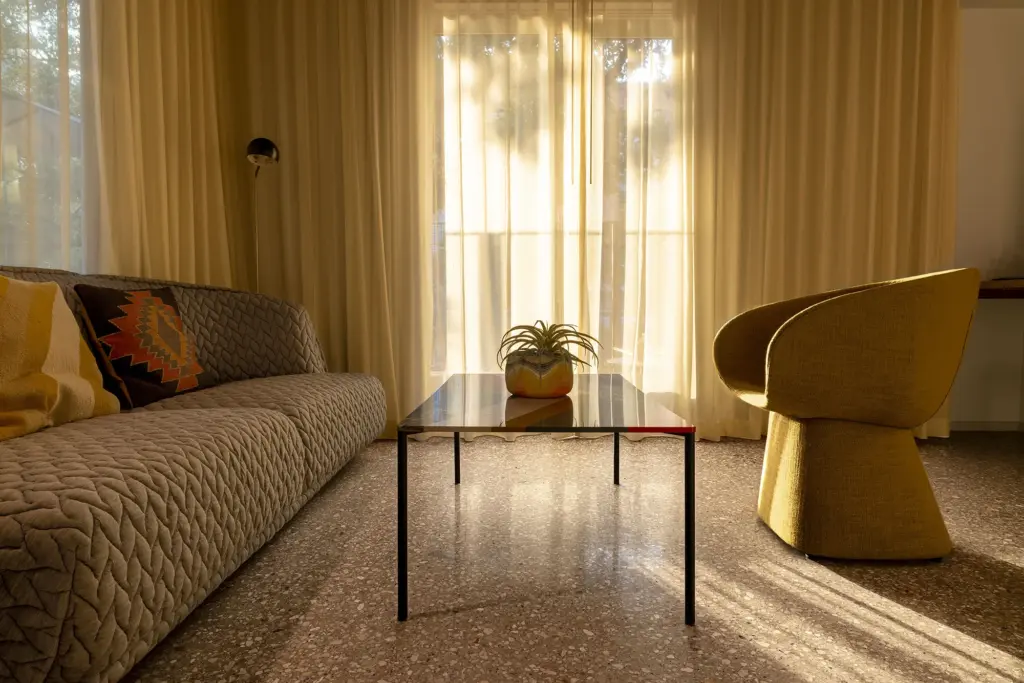
Options for Integrating Color in Concrete Polishing
Integral color is often preferred if it fits within the budget due to its natural appearance and lasting durability. Unlike topical color, an integrally colored slab will never fade or discolor over time, making it a long-term solution. Integrating color into polished concrete is a popular choice for custom home builders, as it helps seamlessly blend the flooring with the overall interior design. It’s important to note that most concrete slabs have tan undertones, not gray. To achieve a cooler, gray-toned floor, adding pigment to the concrete may be necessary.
There are two main ways to add color to polished concrete floors:
- Integral Color – Color is added directly to the concrete mix before pouring.
- Topical Color – Color is applied to the surface after polishing.
While topical color is more affordable and commonly used, it is less permanent than integral color and may require reapplication every five years to maintain its vibrancy.
Our Clients
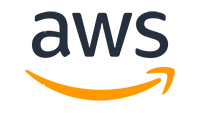
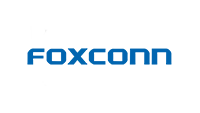
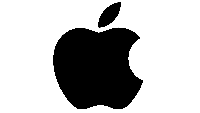
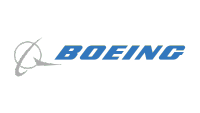
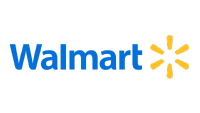
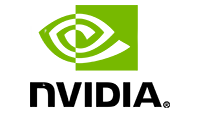
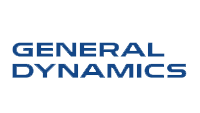
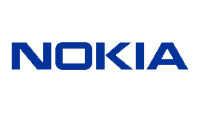
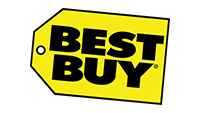
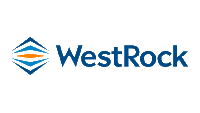
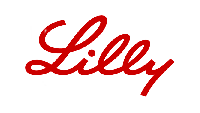

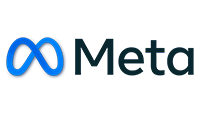
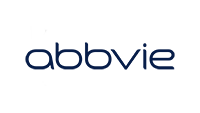
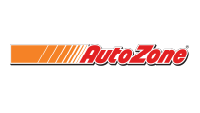
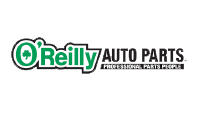
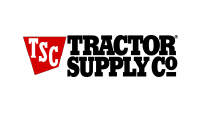
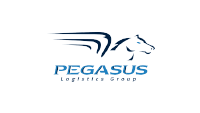
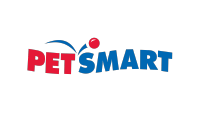
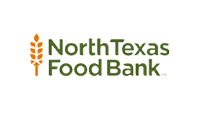
Texas Locations
Colorado Locations
We provides select services outside of these areas. Give us a call for more information.
Blog
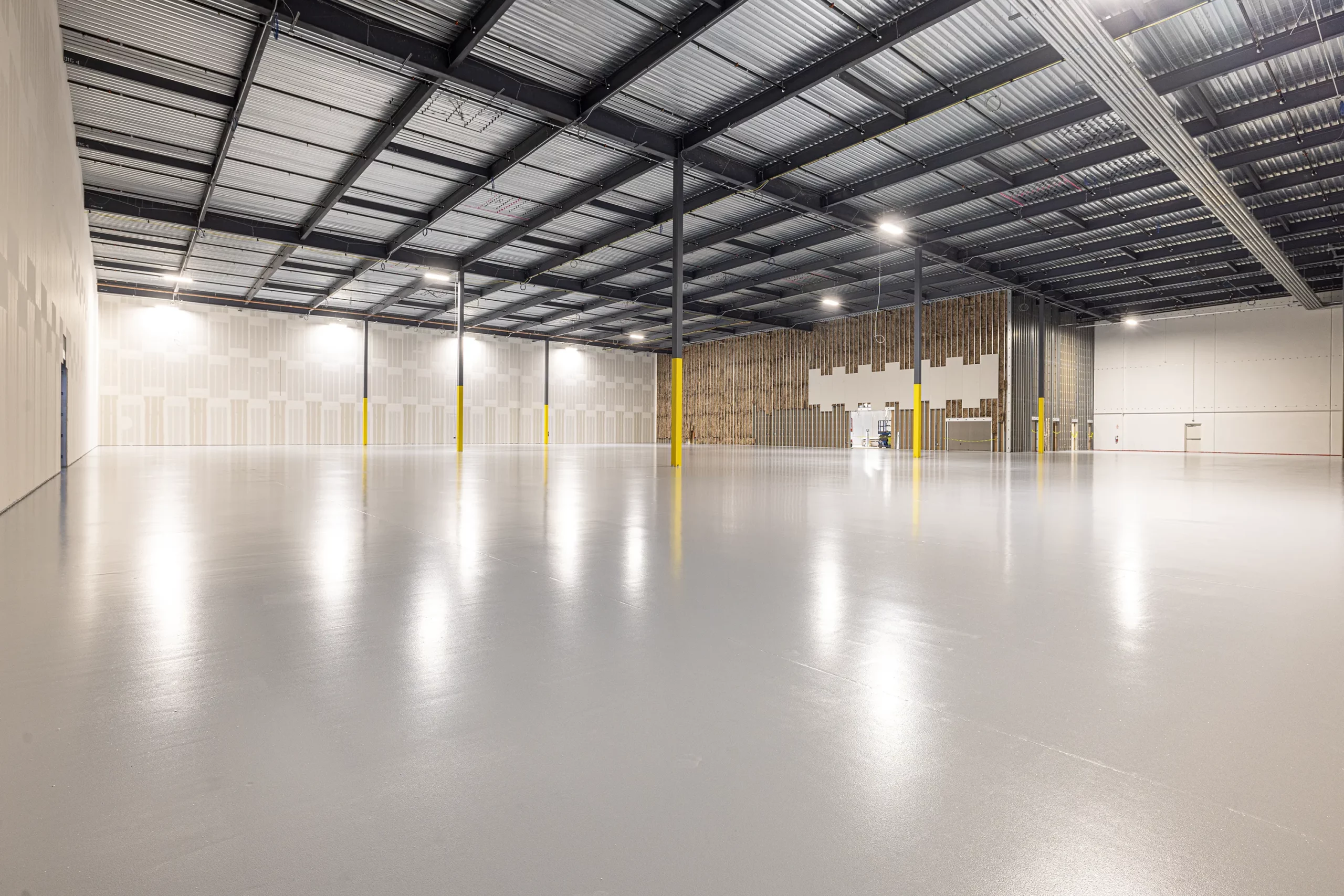
Project Highlight: 34,000 Sq. Ft. ESD Epoxy Installation in Dallas, Texas
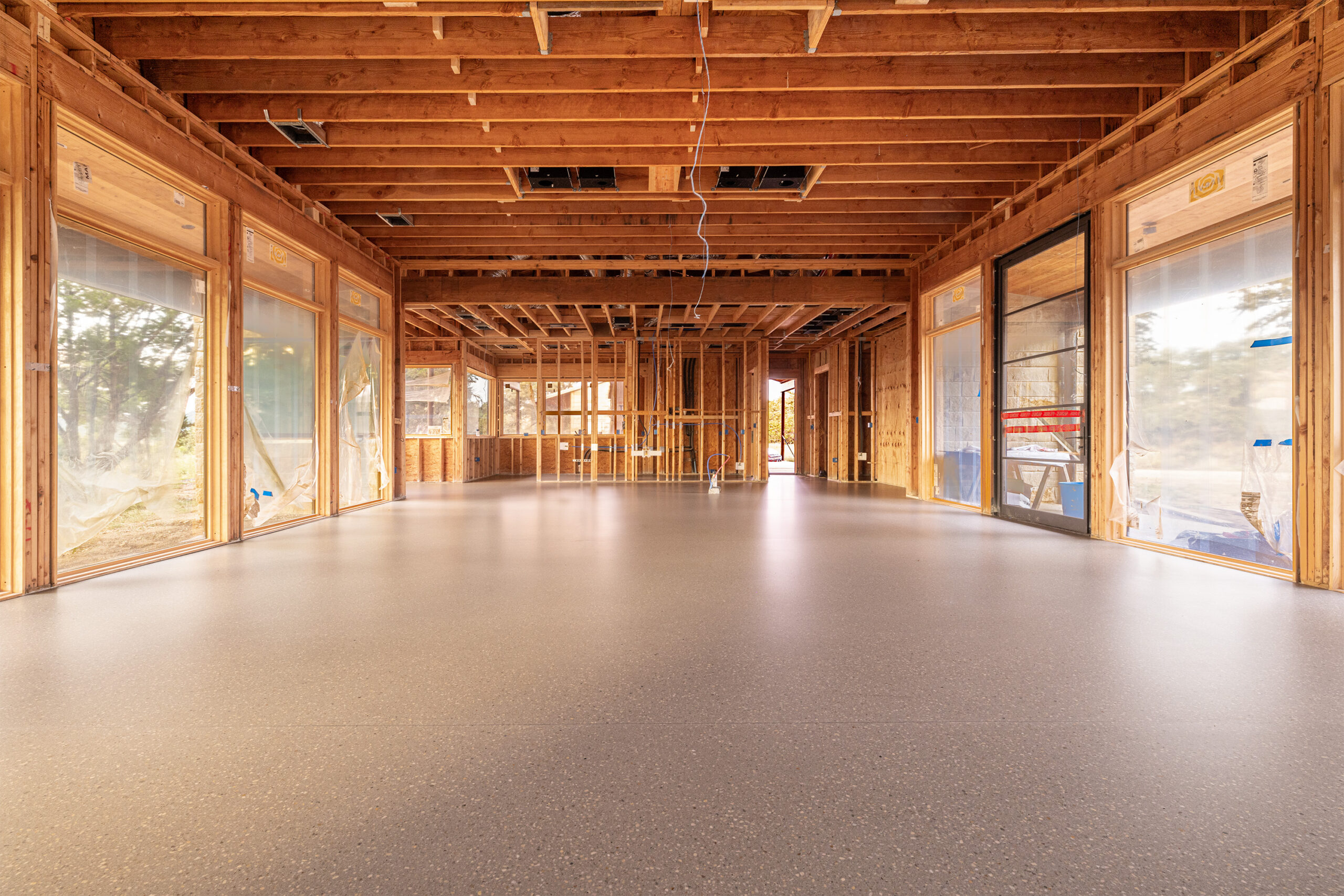
Project Highlight: New Residential Terrazzo Floors in Fort Worth, Texas
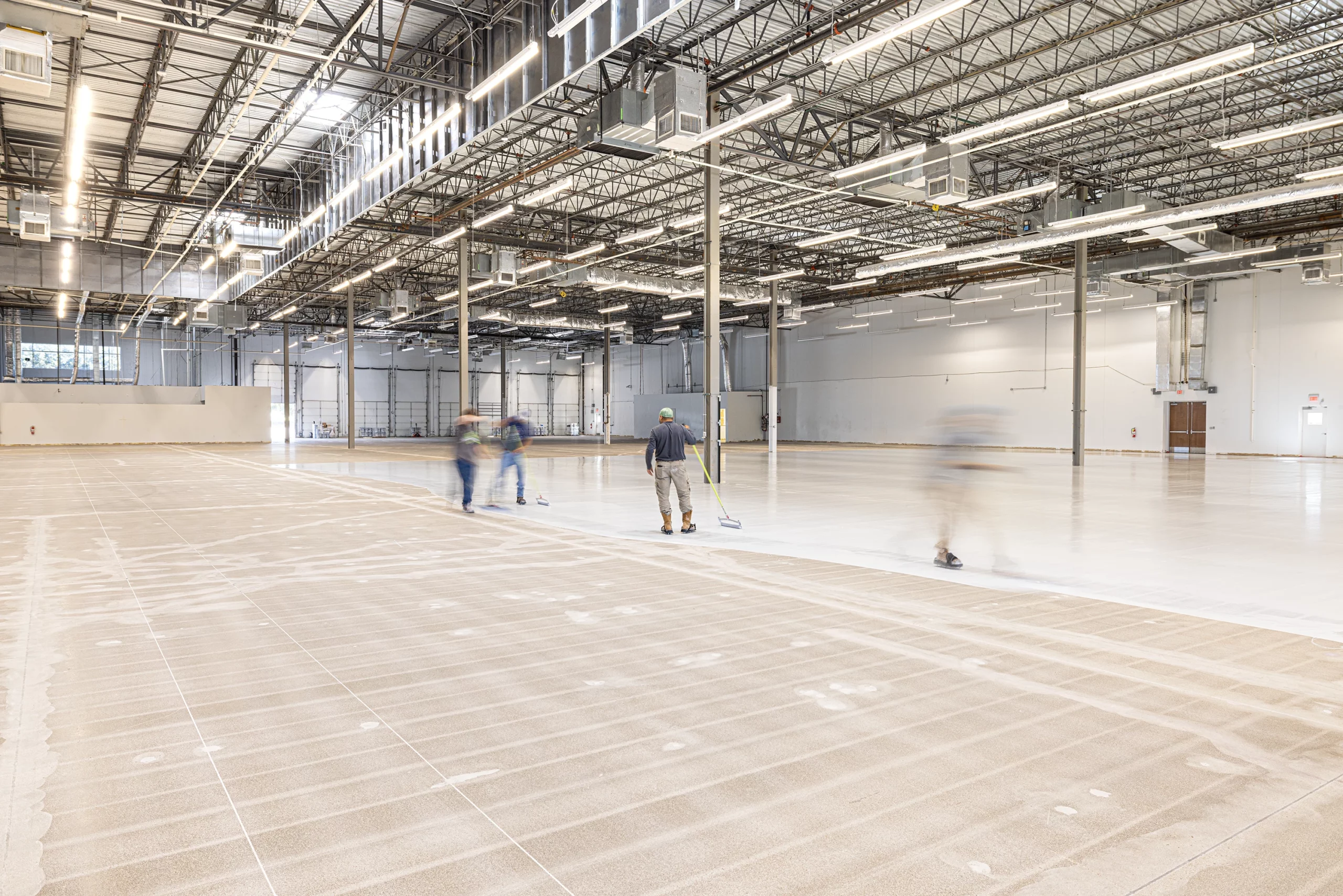