Concrete Flooring Installation Pros and Cons
There are a million different styles of concrete flooring options, and let’s face it, captions under Pinterest pictures do a really bad job of identifying the installation technique you’re admiring. In fact, when having an initial consultation with a new customer, a primary issue we face is that most people have difficulty identifying the finish they desire.
If you can’t decide on whether to seal or polish concrete, It’s not your fault! This is a confusing subject that this page will clear up. These finishes have very different benefits and drawbacks, so it’s really important to have a basic understanding of these finishes before making a decision on a new concrete floor install. This page discusses the differences between sealing and polishing concrete.
The Two Categories of Concrete Floor Finishes
It might be hard to believe, but there are really only two different types of concrete floor finish: sealed concrete and polished concrete.
Sealed concrete, however, is a giant category with a wide variety of options. The most basic sealed concrete floor is simply an acrylic sealer installed over bare concrete, which costs between $1.00 to $1.75 per square foot. However, sealed concrete also includes all types of stained concrete as well as commercial coatings such as epoxy and polyurethane.
Polishing concrete is a very different installation. A polished concrete floor depends on penetrating liquids called silicate densifiers and stain guards to eliminate concrete porosity and prevent staining. Don’t worry if this sounds confusing, we’ll go into more detail on this later. What’s important to keep in mind is that there’s no film covering when you polish concrete floors. As its name suggests, polished concrete is also mechanically honed to achieve the desired level of reflectivity and consistency.
Goals of Sealed or Polished Concrete Floors
Let’s back up a bit and just ask “what are the goals of a sealed or polished concrete floor?”
Fundamentally, the goal of all concrete finishes, whether it’s a sealed or polished concrete floor, is to protect a concrete slab from staining and abrasion.
This is where the major distinction between whether to seal concrete floor or to polish it exists:
Sealed concrete protects a concrete floors by adding a filter over the entire surface, while polished concrete uses penetrating, reactive sealers to prevent staining.
More About Sealed Concrete
Just from reading the content above, it’s easy to come to the conclusion that sealed concrete probably does a better job of protecting a floor from staining than polished concrete. In most cases that’s correct, however, sealed concrete has some serious drawbacks that must be considered. We’ll discuss these more later, but here’s a very basic overview of the benefits and drawbacks of a sealed concrete floor.
BENEFITS OF SEALED CONCRETE
- High stain and chemical resistance
- Fast install time
- High gloss
- Cost effective for basic installations
DRAWBACKS OF SEALED CONCRETE
- High potential for failure
- Difficult or impossible to repair
- Quickly shows scratches and wear patterns
- Slippery, especially when wet
To learn more about sealed concrete, visit our main ‘sealed concrete floors‘ page
When to install Sealed concrete floors
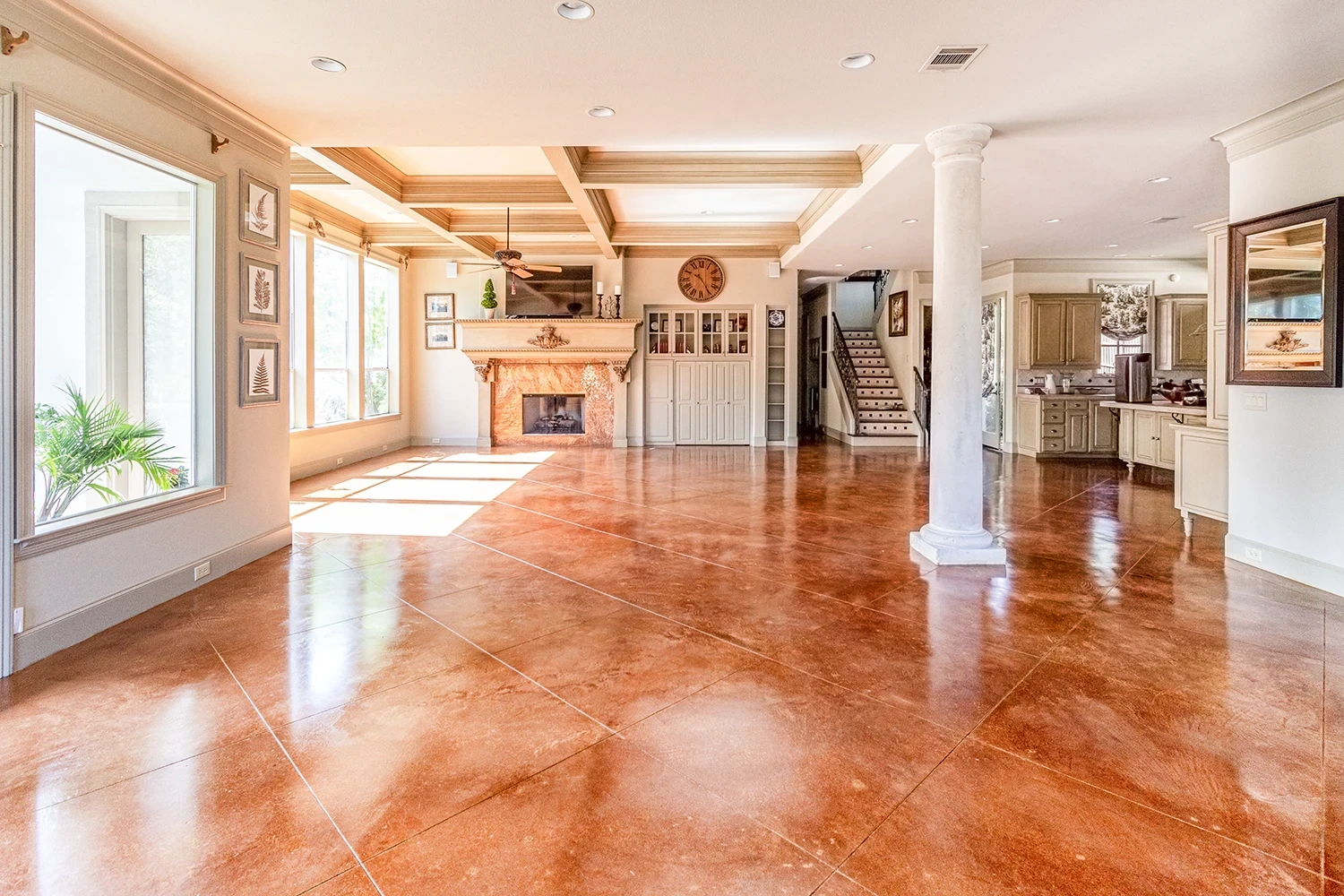
STAINED CONCRETE
When most people think of a concrete floor, they think of stained concrete. This is primarily due to the fact that this installation has been around for over 100 years. However, it might surprise you to learn that only a small fraction of new residential concrete installations are stained concrete. Stained concrete always requires a concrete floor sealing coat to prevent the color from wearing off, so it should functionally be considered sealed concrete—it has the same set of benefits and drawbacks.
Looking for more Information About Stained Concrete? Visit our main ‘stained concrete floors‘ page
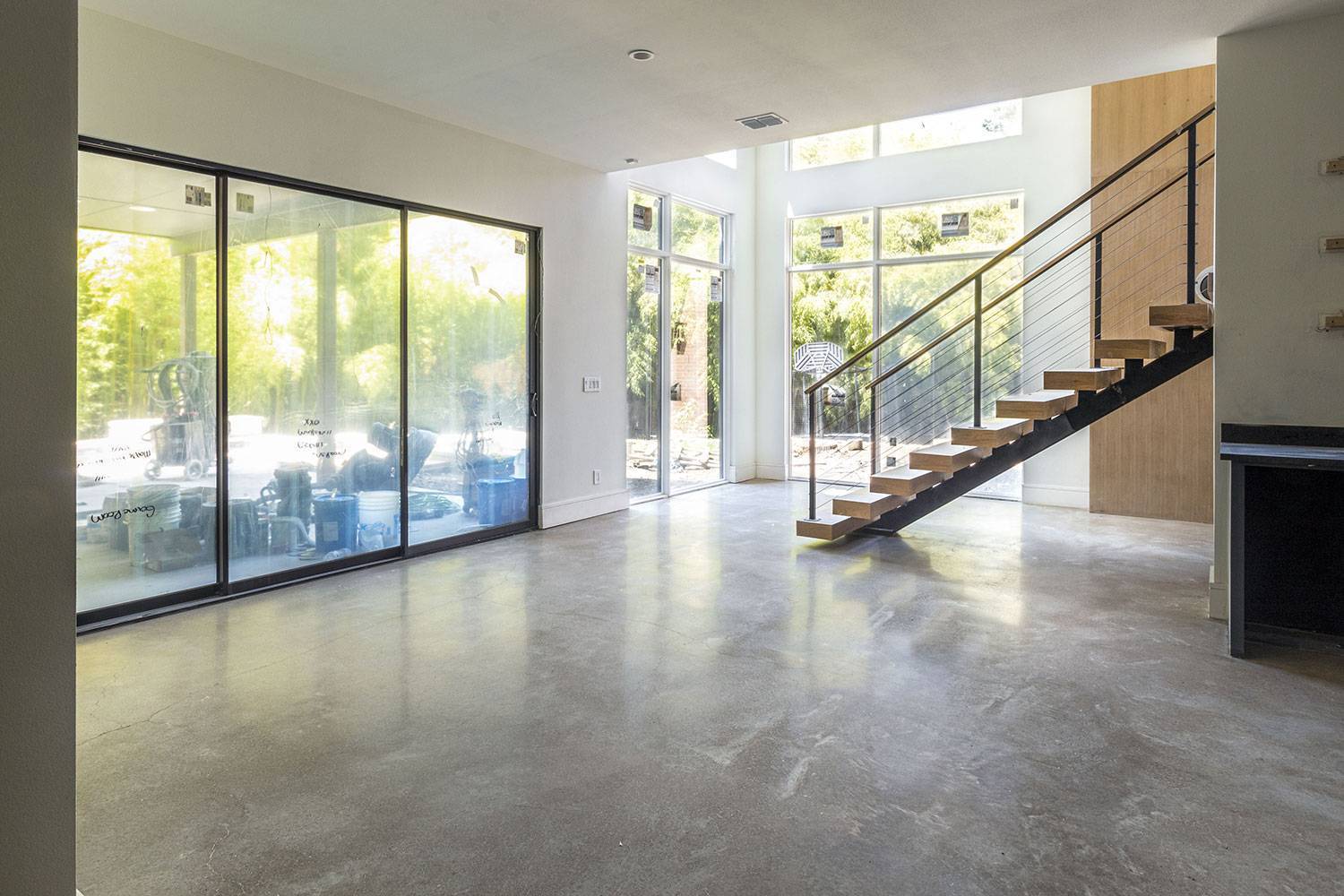
Basement Concrete Floors and Foundation Walls
When sealing a basement floor, applying a waterproof basement floor sealer is an absolute necessity. Foundation walls and the concrete basement floor need waterproofing sealers to lock out moisture and protect the foundation of your house. An epoxy coating makes a perfect basement concrete floor sealer to maintain and preserve your space.
How to Seal Concrete Floor in The Basement?
When opting for an epoxy coating for your basement floor, be sure to apply the epoxy to a cool floor, which will help it stick to the surface. Choose a long-handled roller to apply a thin coat of epoxy. If you need a second coat, be sure to allow the first coat to dry for 24 hours before applying the second.
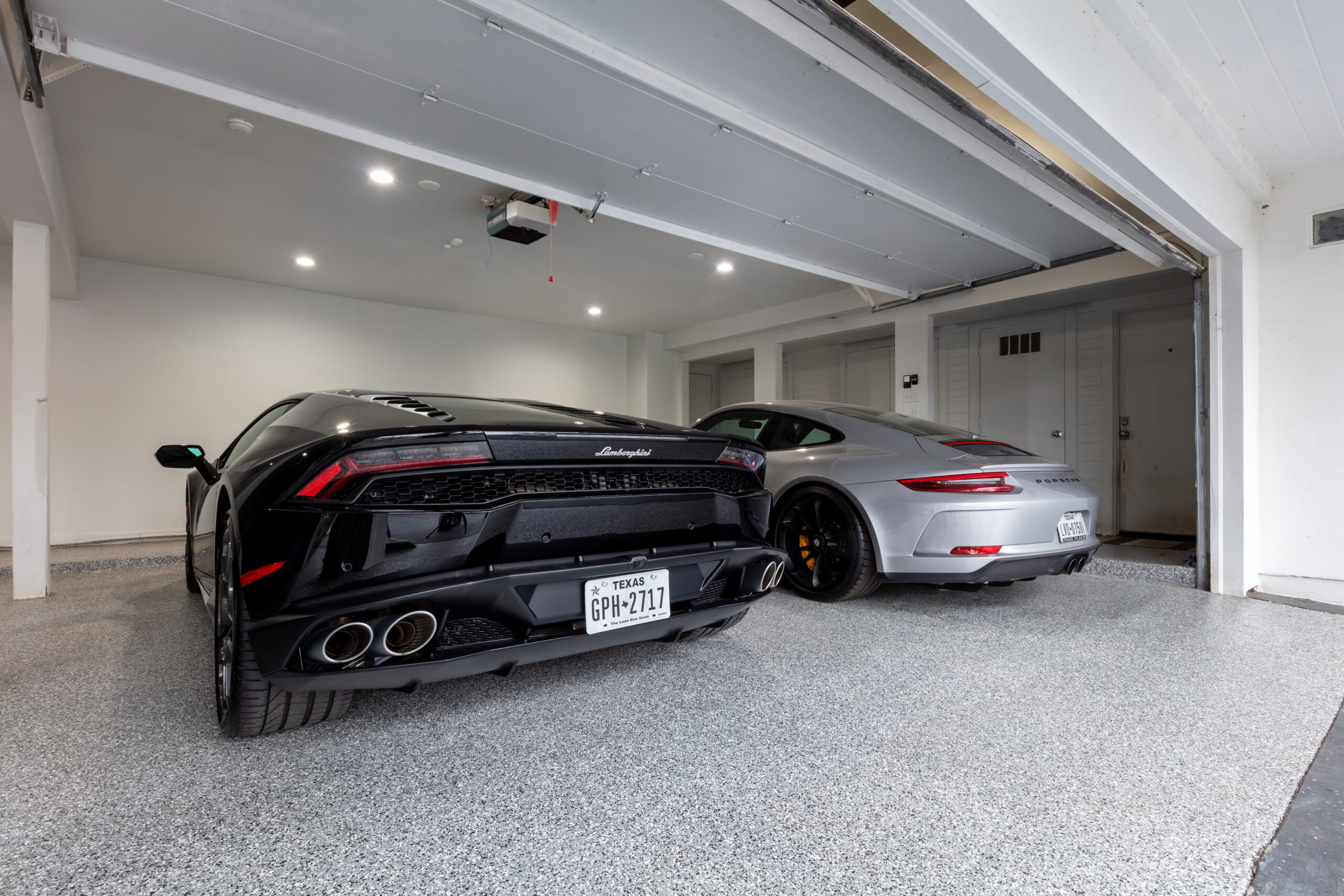
GARAGE FLOORS
At Craftsman Concrete, we regularly install both sealed and polished concrete in residential garages. To settle the debate of polishing a concrete floor vs coating it with epoxy for your garage floor, it depends on whether your project is new construction and how you’ll be using your garage. If you’re a gearhead, hobbyist mechanic, or have cars that might leak fluids, then epoxy, a high-quality garage floor sealing coat, is absolutely the installation for you.
Polished concrete can only be installed in garages that are new construction. Garages that have already seen significant vehicle traffic are often already too stained or worn for a proper polishing process.
Need garage floor inspiration? Visit our ‘garage floor data sheets‘ page
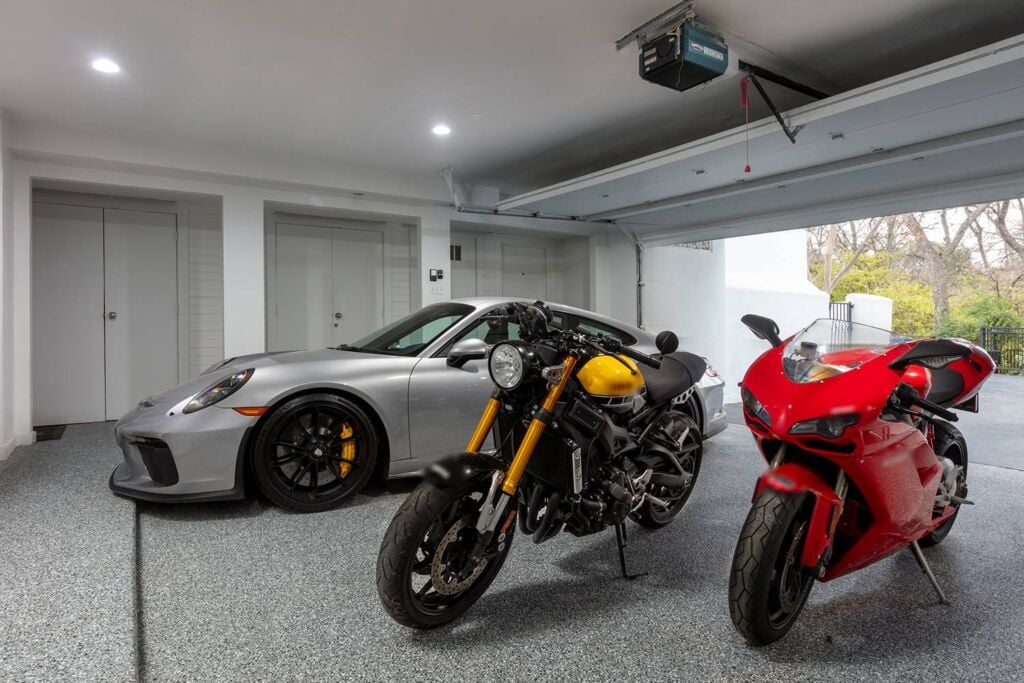
More About Epoxy Garage Floors
Luxury epoxy garage floors are generally installed as a three-part system: a 100% solids epoxy base coat, a coat of epoxy flakes with 100% coverage, and a polyurethane topcoat. While this can start to get a bit technical, there’s one giant advantage that these floors have that other sealed concrete floor don’t—they’re repairable. Because of the epoxy flake layer, if an epoxy garage floor is scratched to the point of being damaged, new epoxy flakes and polyurethane topcoats can be seamlessly installed. While this type of damage is exceedingly rare, this characteristic makes epoxy flake the most durable installation for garages that will see serious use.
Visit our ‘epoxy flooring cost‘ page for more about this installation.
In depth Drawbacks of Sealed Concrete
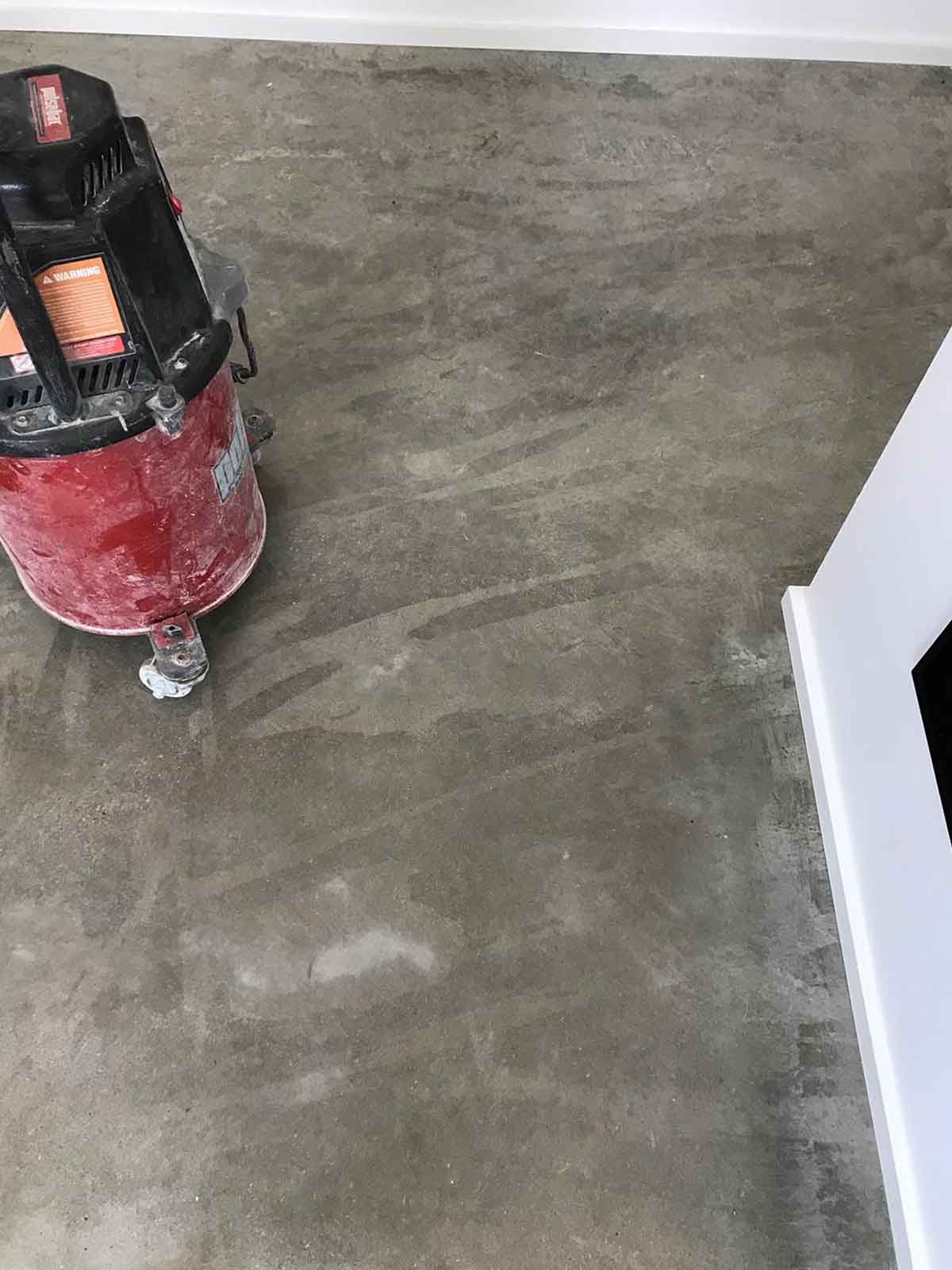
SEALED CONCRETE FLOORS CAN FAIL
The most critical drawback of sealed concrete is its high potential for failure.
You’re probably asking, ‘how does a sealed concrete floor fail?’ In most cases, the sealer simply starts to separate from the concrete it was applied to. To make things worse, in nearly all cases of failure the entire floor must be resurfaced and resealed in order to achieve an aesthetic appearance. Sealed concrete is simply not a repairable concrete floor installation.
Of the various reasons concrete sealers fail, the most common is poor preparation of concrete surfaces.
Concrete preparation requires specialized equipment, so it’s generally not possible for anyone other than a concrete floor installer to properly install a sealed concrete floor. In fact, even with proper preparation, a sealed concrete floor generally has a much shorter lifespan than a polished concrete floor.
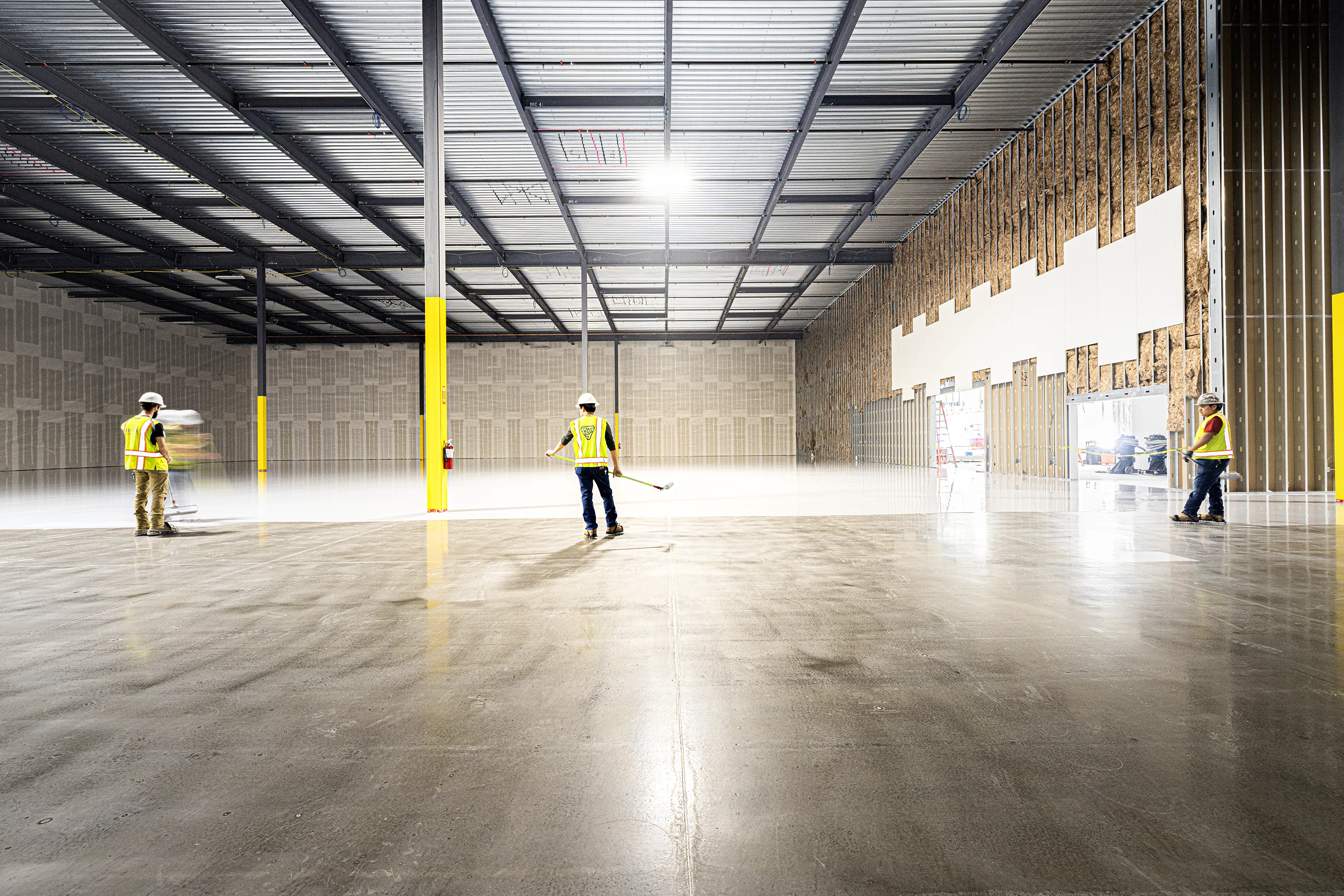
Excessive Vapor Pressure
The other primary reason sealed concrete flooring fails is due to excessive vapor pressure in the concrete slab. While this is a very technical subject that’s outside the purview of this article, this failure is the result of moisture in the concrete becoming trapped under the sealer. Here in Texas, where it’s extremely humid, these types of failures aren’t uncommon.
Polished concrete floors do not fail due to excessive moisture. Because the polishing process of concrete floors does not include a surface film, polished concrete flooring releases moisture naturally without any impact on their finish.
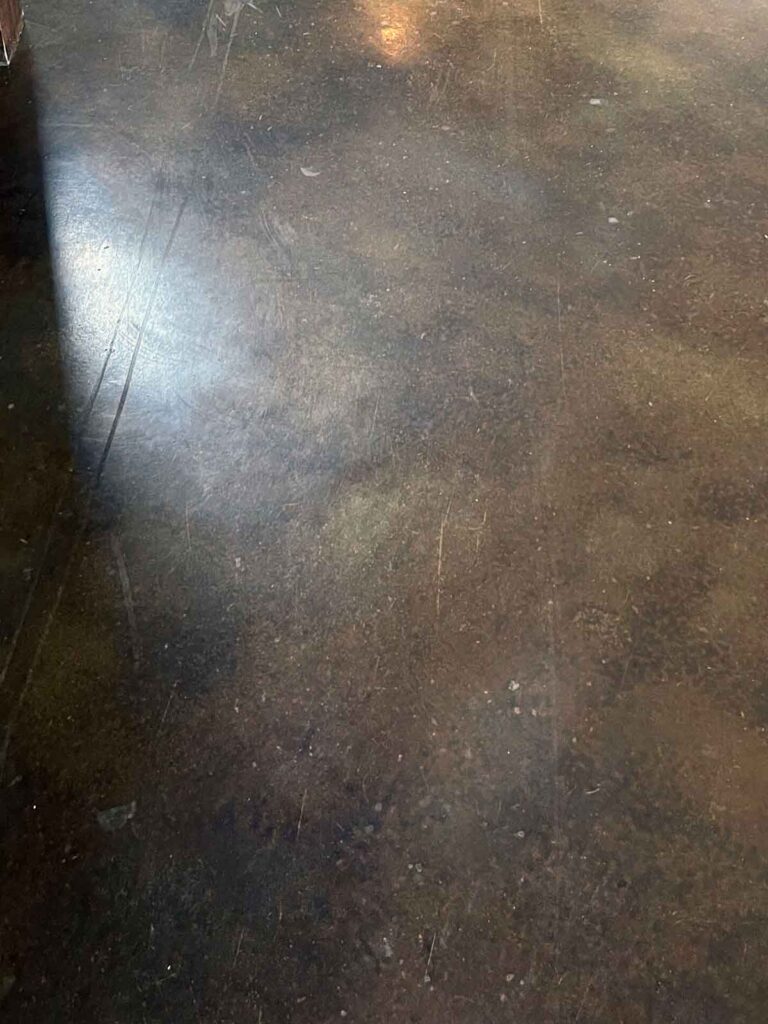
SCRATCHING AND OTHER WEAR
Another major drawback of sealed concrete flooring is their propensity for showing scratches and wear in high foot traffic areas. This is due to the fact that the coating on top of the concrete simply isn’t as durable as the concrete it’s bonded to. Over time, this coating is slowly worn down to the underlying concrete slab, leaving unsightly wear patterns in high traffic areas. No matter the type of floor or variety of concrete sealer, some scratching and wear should be expected on a sealed concrete floor.
SEALED CONCRETE FLOORS ARE EXPENSIVE TO REPAIR
We frequently get phone calls from residential customers who tried to save money by having sealed concrete installed by an unqualified contractor or they took it as a DIY project, only to have the sealer start to fail shortly after installation.
Unfortunately for these homeowners, they often ind that repairing their floors costs many times what the initial installation did. For most sealed concrete failures, the entire floor must be stripped or ground and a new coat of sealer applied. This is much more labor-intensive than the initial installation and will cost you money per square foot!
In most cases, after the failure of a sealed concrete floor, our customers decide to switch to a polished concrete installation. While the upfront cost per square foot is higher, when you polish concrete floors properly, they cannot fail and require little to no maintenance.
More about Polished Concrete
If you’re a residential builder or homeowner considering a concrete floor, pay attention to this statistic—over 95% of our residential customers choose to polish concrete for their interior floors. A polished concrete floor simply looks better, lasts longer than a sealed concrete floor, and costs between $3.5 to $5 per square foot. Below is a very basic overview of the benefits and drawbacks of a polished concrete floor.
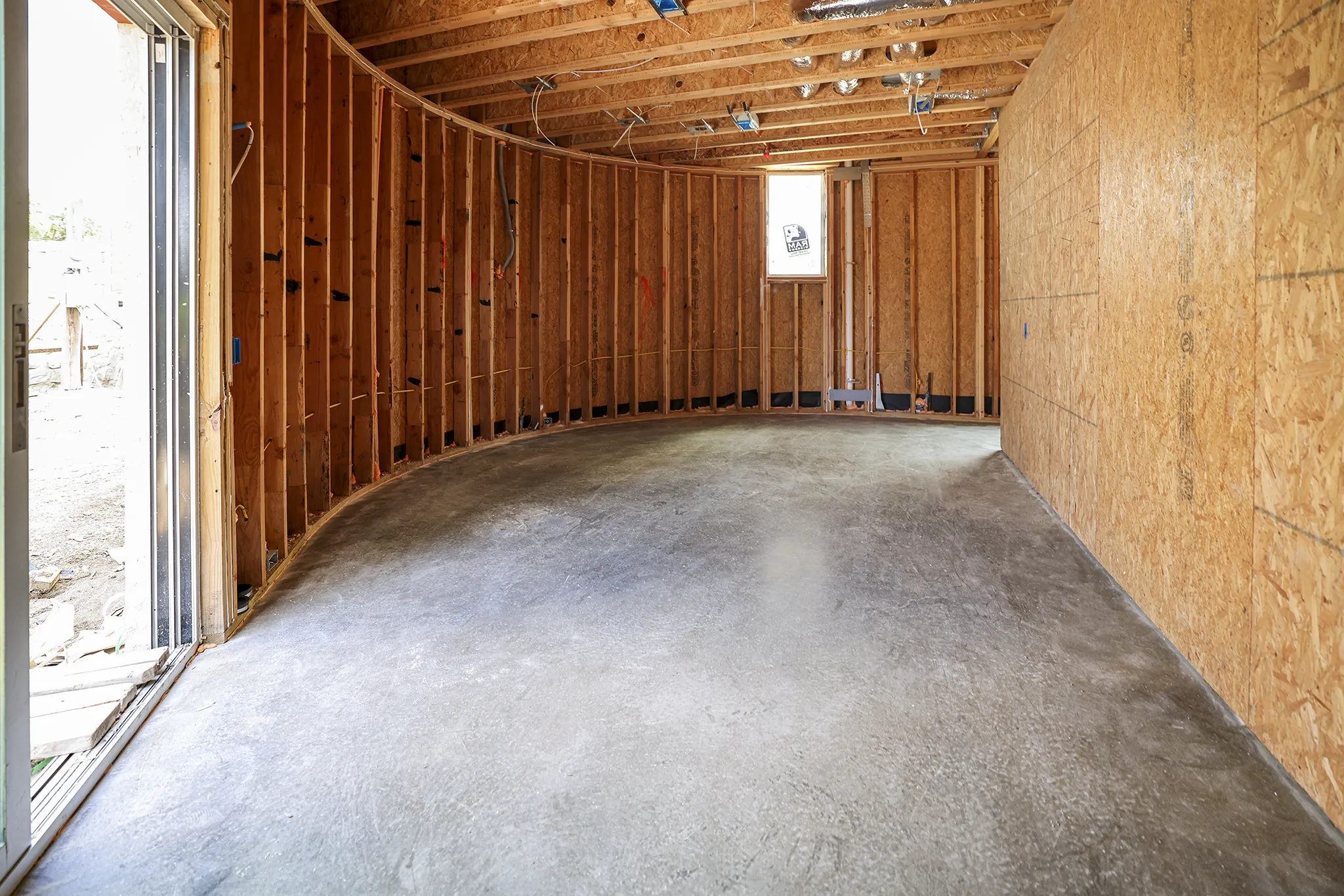
BENEFITS OF POLISHED CONCRETE
- Extremely high durability and low maintenance
- Natural, beautiful appearance
- Extremely high slip resistance
- Gloss levels from matte to high gloss mirror
- No volatile chemicals used during installation
- Finished by only a power trowel or a hand trowel. No sealing is required.
DRAWBACKS OF POLISHED CONCRETE
- Lower stain resistance
- Slower installation time
- Higher installation cost per square foot (Less cost effective)
- Less well suited for certain industrial and exterior installations
To learn about polished concrete pricing, visit our ‘polished concrete cost guide‘
Blog

Project Highlight: 34,000 Sq. Ft. ESD Epoxy Installation in Dallas, Texas
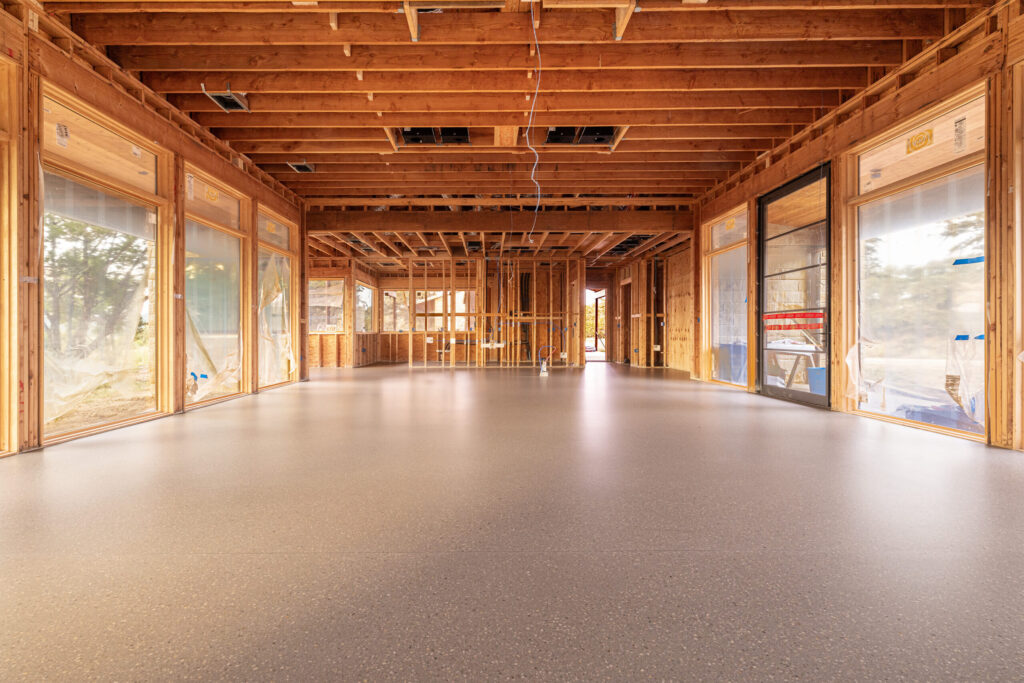
Project Highlight: New Residential Terrazzo Floors in Fort Worth, Texas
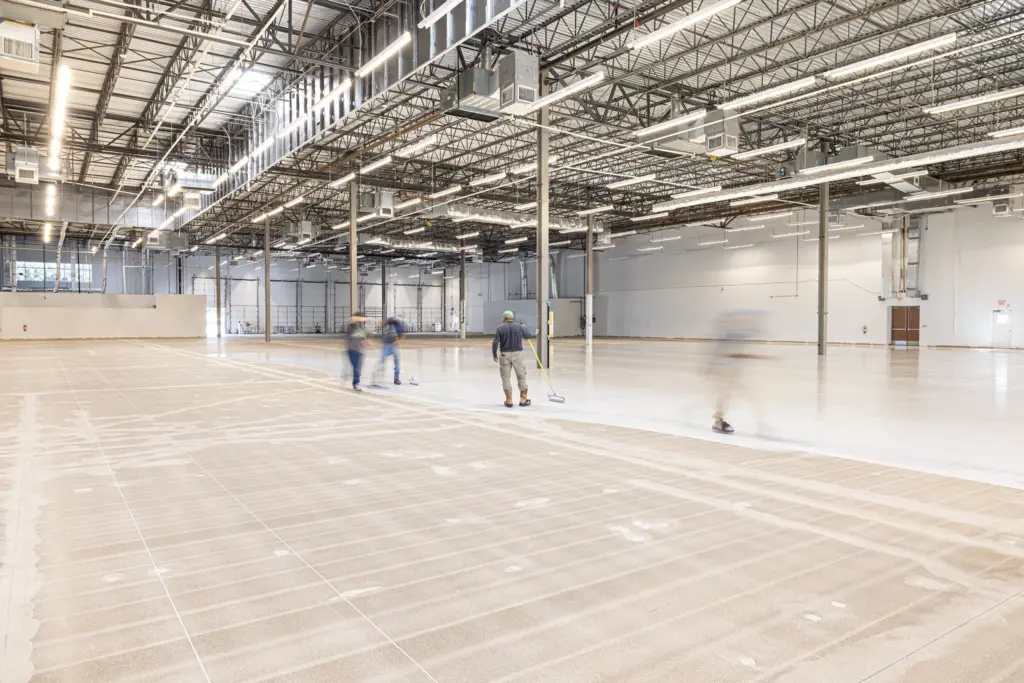